Poly(butylene adipate-co-terephthalate) (PBAT)/AgFe2O4 biopolymer nanocomposite-based flexible triboelectric nanogenerator as a self-powered touch sensor
Vishnu Kadabahalli Thammannagowda, Kariyappa Gowda Guddenahalli Shivanna, Smitha Ankanahalli Shankaregowda, Stéphane Panier, Prashantha Kalappa

Vol. 19., No.7., Pages 670-685, 2025
DOI: 10.3144/expresspolymlett.2025.51
DOI: 10.3144/expresspolymlett.2025.51
GRAPHICAL ABSTRACT
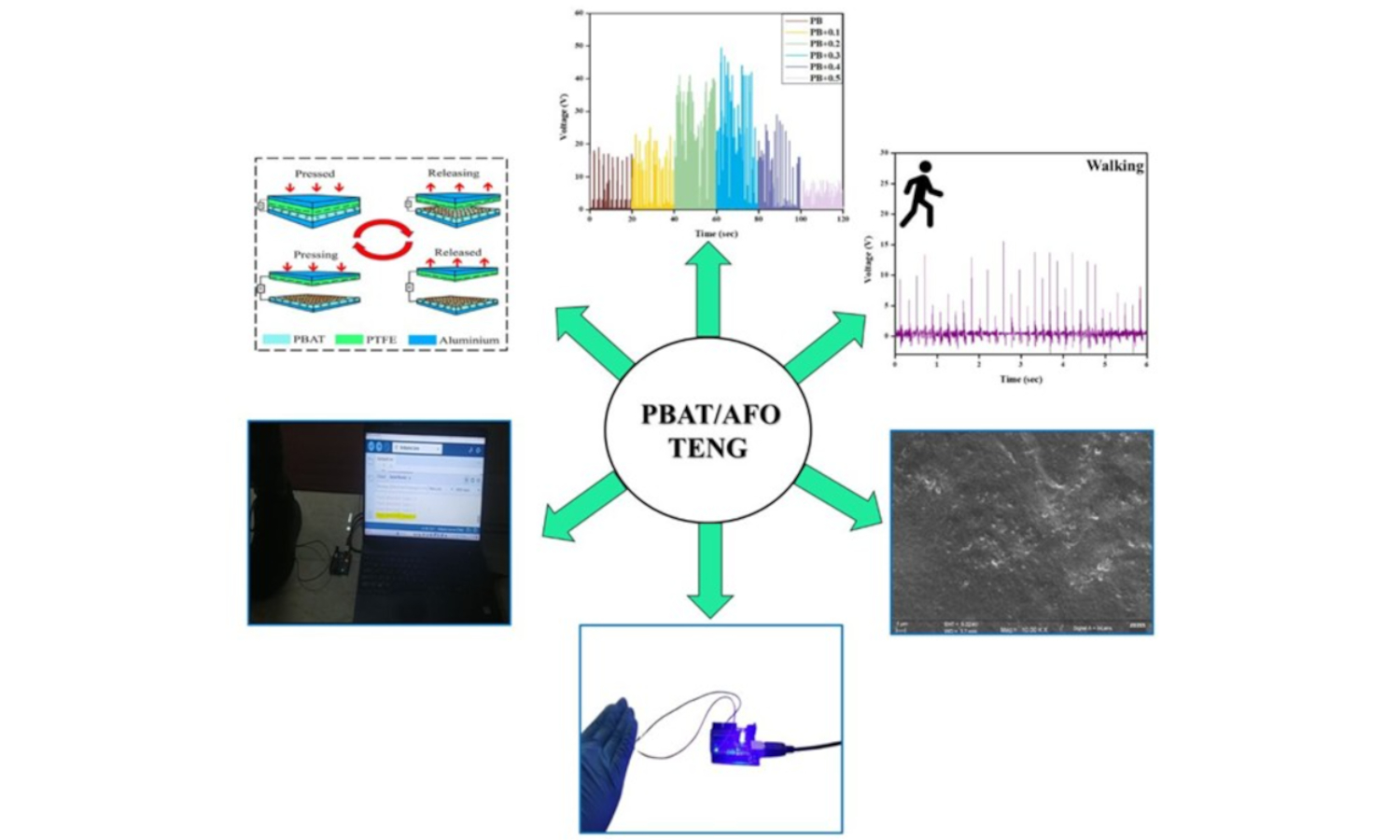
ABSTRACT
Triboelectric nanogenerators (TENGs) offer a promising solution for self-powered sensor applications, but their viability depends on cost-effective and efficient designs. This study presents a simple, durable, low-cost, and biodegradable poly(butylene adipate-co-terephthalate)/AgFe2O4 (PBAT/AFO) based TENG, utilizing an innovative approach towards environmental sustainability. AgFe2O4 (AFO) nanoparticles, synthesized via combustion, were characterized using X-ray diffraction (XRD) and Fourier transform infrared (FTIR) spectroscopy. Synthesized AFO nanoparticles were then incorporated into PBAT to prepare polymer nanocomposite, with scanning electron microscopy (SEM) confirming their uniform dispersion. Electrical performance evaluations demonstrated efficient charge transfer, yielding a maximum output voltage of 49.15 V and a current of 4.9 μA under hand tapping. The PBAT/AFO-TENG successfully powered LEDs and an electronic calculator, showcasing its practical utility. Additionally, it functioned as a self-powered biomechanical sensor for human body motion detection, touch security, and touch counter for laboratory entry tracking. This work highlights the simplicity, environmental sustainability, cost-effectiveness, and versatility of PBAT/AFO-TENGs, positioning them as promising candidates for future portable electronics and sensing applications.
RELATED ARTICLES
Kai Du, Qiang Ben, Xiaoqiang Wang
Vol. 19., No.8., Pages 796-808, 2025
DOI: 10.3144/expresspolymlett.2025.61
Vol. 19., No.8., Pages 796-808, 2025
DOI: 10.3144/expresspolymlett.2025.61
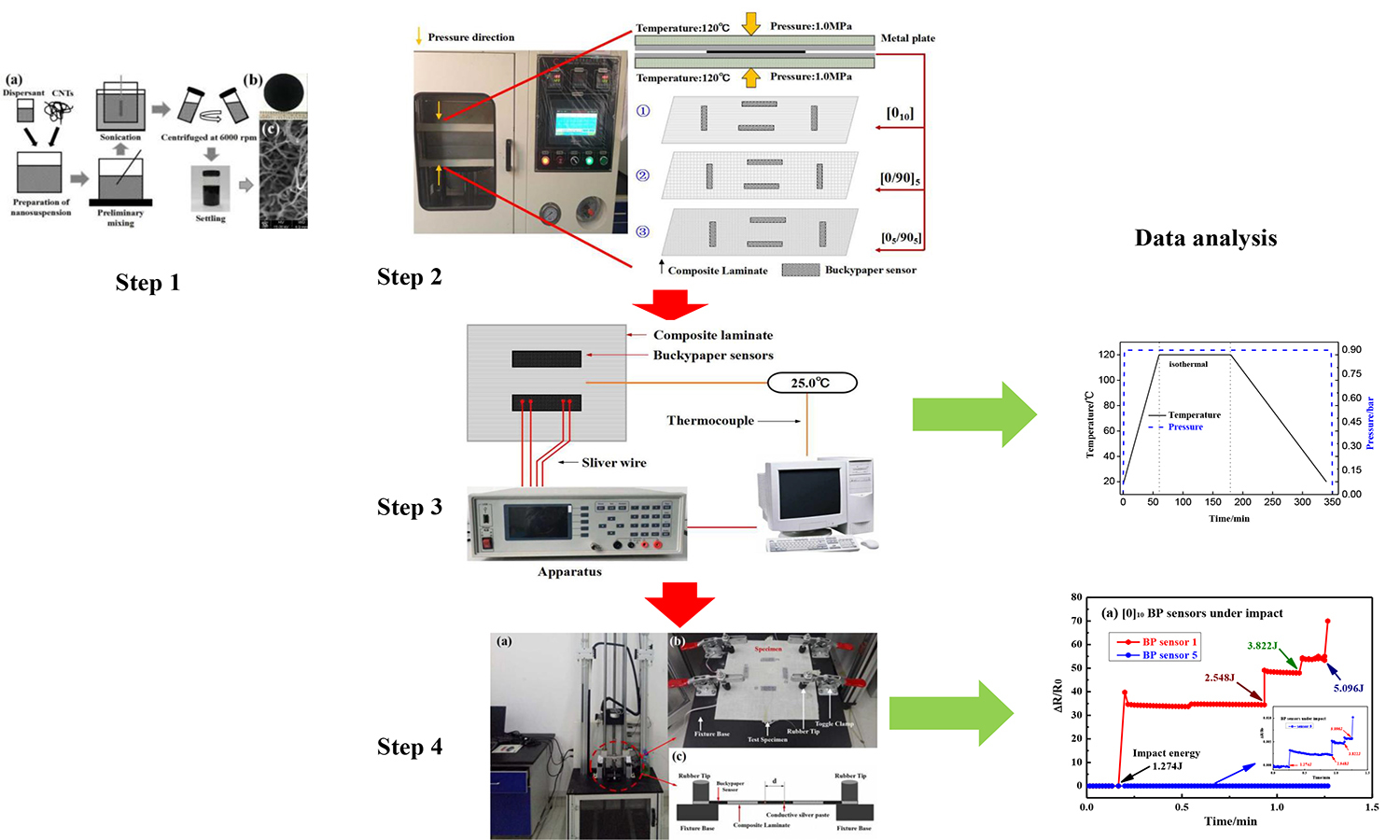
The main purpose of structural health monitoring (SHM) is to detect damage at its earliest possible stage to prevent severe deterioration and reduce subsequent repair costs. Carbon nanotubes (CNTs) buckypaper (BP) was embedded into different cross-ply glass fibre composites to monitor the curing process and impact damage as an in situ sensor in this research. BP sensor can capture the four stages of the curing process, the gel point of the resin and residual stresses of the composite structure can be achieved by analysing the change of the resistance curve. Numerical and experimental analyses were performed to predict the damage in composite structures subjected to low-velocity impact. BP sensors’ electrical resistance increases with repeated impact loading; composite structure elastic deformation and damage evolution can be identified from resistance change. Experiment results show that structure monitoring based on the BP sensors cannot only detect small, barely visible impact damage flaws and the damage evaluation of composite structures subjected to impact, but also provide a new method to monitor the curing process through the analysis of results. This work makes some constructive contributions to monitoring the manufacturing process of composites and long-term SHM to evaluate impact resistance and damage prediction of composite structures.