High-performance polyimide fiber by low-temperature thermal imidization from polyamic acid precursor fiber via dry-jet wet-spinning
Vol. 19., No.5., Pages 531-543, 2025
DOI: 10.3144/expresspolymlett.2025.39
DOI: 10.3144/expresspolymlett.2025.39
GRAPHICAL ABSTRACT
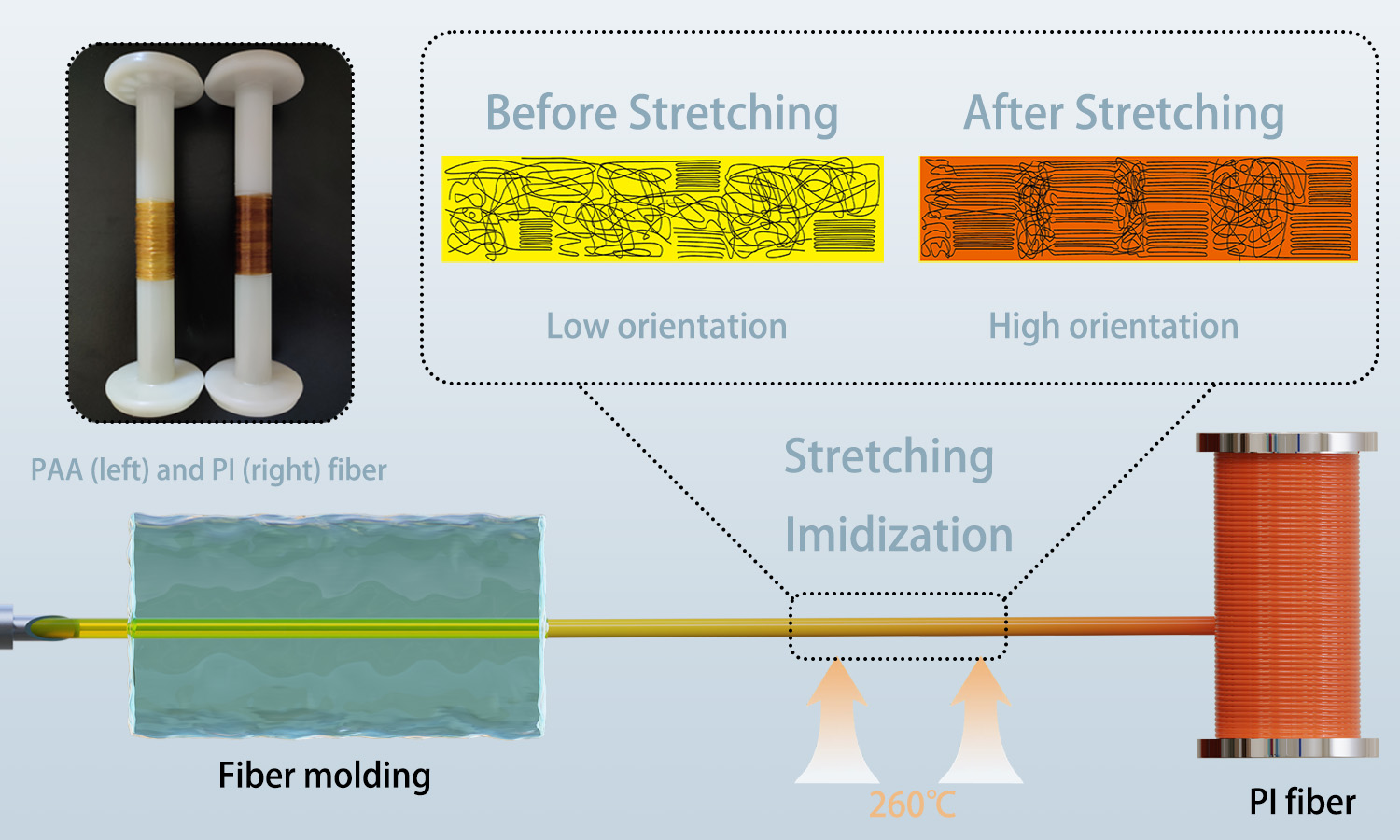
ABSTRACT
Polyimide (PI) fiber is a promising and high-performance polymer fiber with high temperature resistance and low density; however, much energy is needed during the thermal imidization process. Here, PI fiber with excellent mechanical properties and high-temperature resistance was fabricated via the dry-jet wet spinning method for polyamic acid (PAA) precursor fiber, followed by stretching and thermal imidization reaction at a lower temperature. With the increase of the stretching ratio, the mechanical properties of the PI fiber increase significantly. When the stretching was twice as long, the tensile strength and initial modulus of the fiber were as high as 6.23 and 114.13 cN·dtex–1, respectively. Fourier transform infrared results revealed that all samples were completely imidized at 260 °C. The resulting PI fibers exhibit only 5% weight loss at 539.53 °C, and its limiting oxygen index (LOI) can reach up to 32.6%, showing excellent high temperature resistance and flame-retardant properties as well as commendable mechanical performance, which compare favorably with those of other imidization methods.
RELATED ARTICLES
Quentin Watel, Aurélie Cayla, Fabien Salaün, François Boussu
Vol. 19., No.5., Pages 494-503, 2025
DOI: 10.3144/expresspolymlett.2025.36
Vol. 19., No.5., Pages 494-503, 2025
DOI: 10.3144/expresspolymlett.2025.36
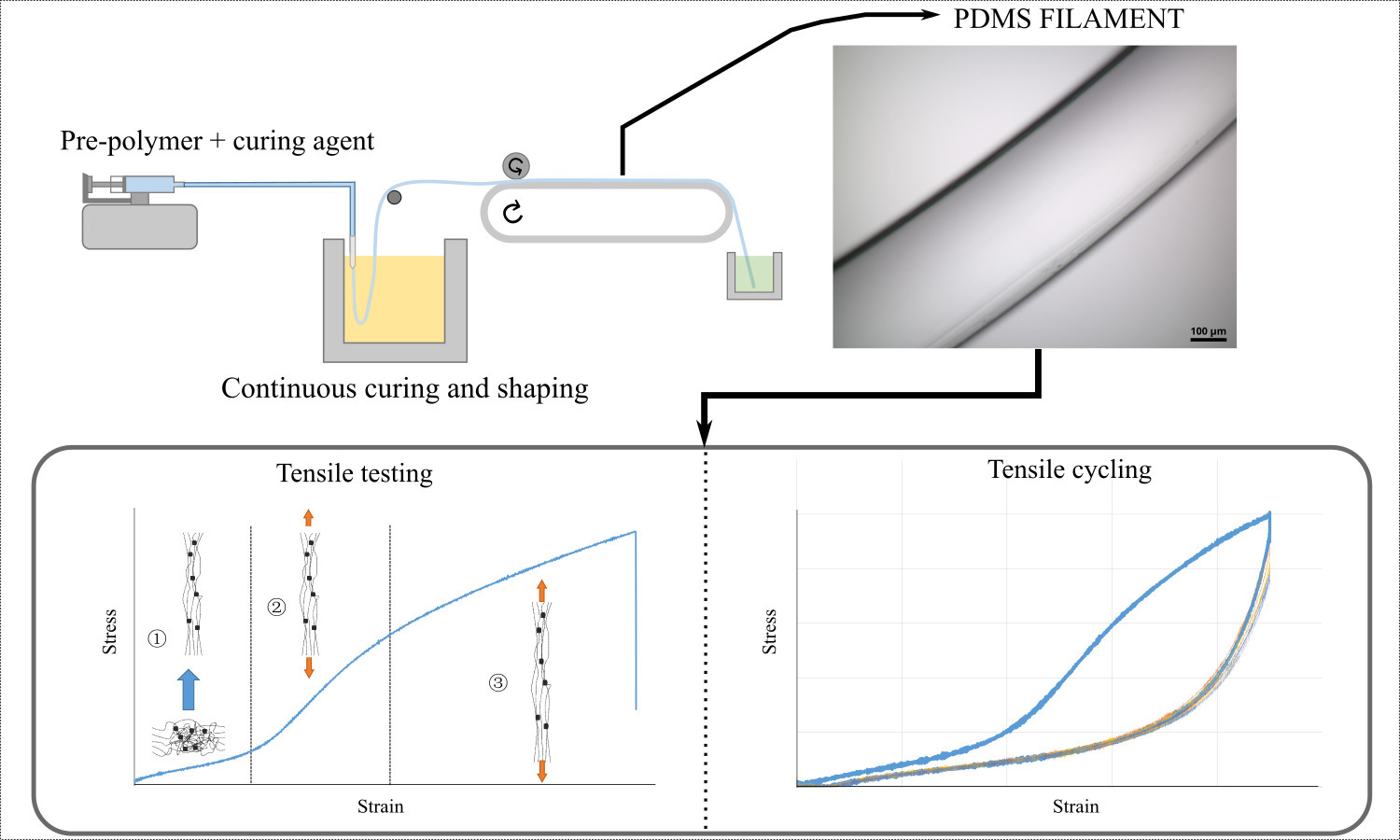
In this work, a PDMS spinning technique is developed and enables the continuous production of a filament with a circular cross-section (~500 μm diameter). The production of continuous silicone polymer filaments can be useful in the textile field to provide new properties in applications such as weaving, knitting or composite reinforcement. The method involves injecting the pre-polymer and curing agent mixture into a heated oil bath (202–215 °C) to simultaneously shape and cure the PDMS. The morphological and mechanical properties of the filament are studied regarding the production parameters (formulation, needle diameter, bath temperature, conveyor belt speed). The most homogeneous filament is produced at the highest temperature (215°C) and conveyor belt speed (13.6 m∙min–1). When subjected to cyclic mechanical stress, the PDMS filament produced exhibits stable mechanical behavior, making it suitable for a wide range of applications.
Konstantin Vadimovich Malafeev, Olga Andreevna Moskalyuk, Vladimir Evgenyevich Yudin, Dmitry Nikolayevich Suslov, Elena Nikolaevna Popova, Elena Mikhaylovna Ivan’kova, Alena Alexandrovna Popova
Vol. 18., No.3., Pages 296-308, 2024
DOI: 10.3144/expresspolymlett.2024.21
Vol. 18., No.3., Pages 296-308, 2024
DOI: 10.3144/expresspolymlett.2024.21
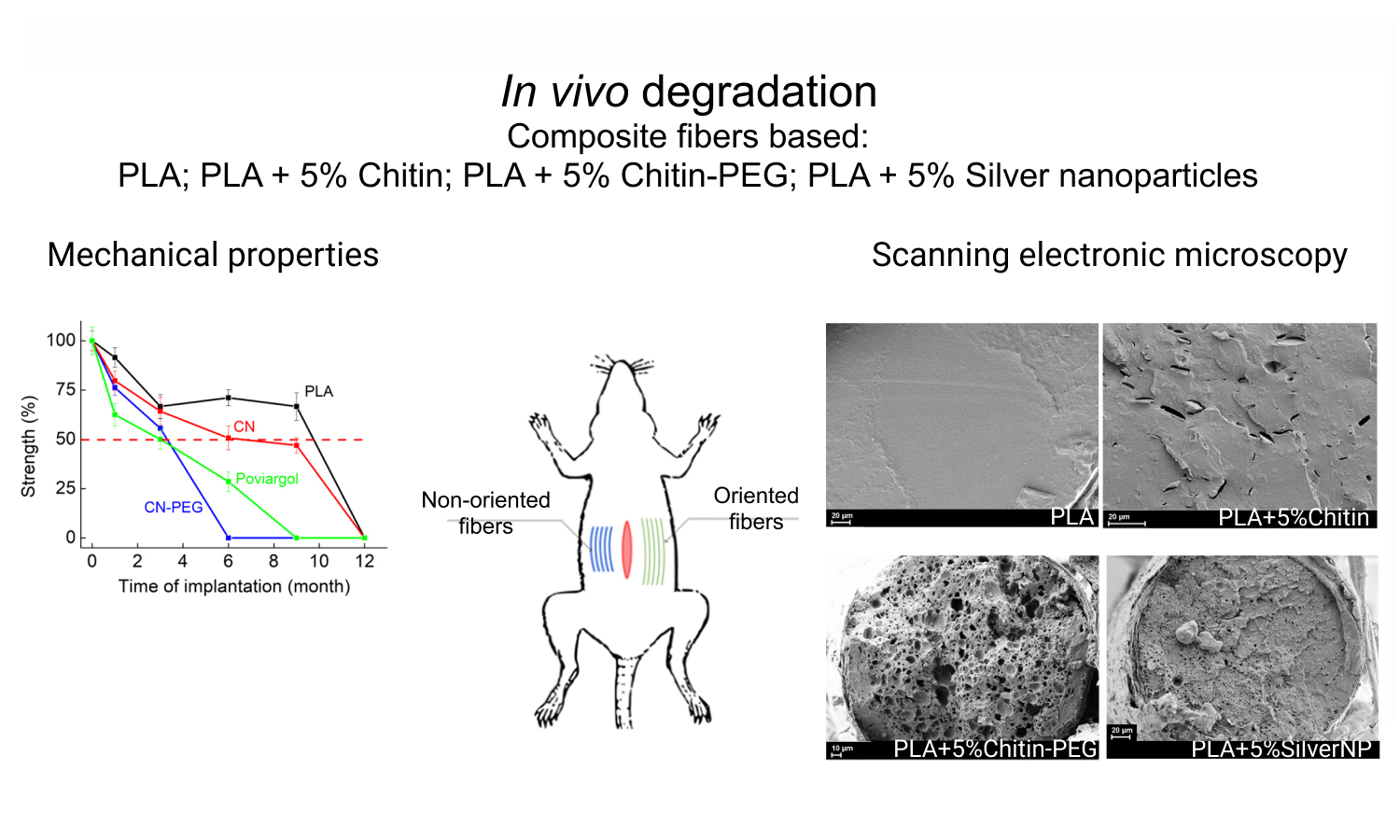
The rates of in vivo bioresorption of composite monofilaments based on polylactide (PLA) containing chitin nanofibrils of two types (pure chitin (CN) or chitin modified with poly(ethylene glycol) (CN-PEG)) or silver nanoparticles stabilized with poly(N-vinylpyrrolidone) (Poviargol) were studied. The in vivo bioresorption rate and its dependence on the degree of orientational drawing of the samples (which varied from 1 in non-oriented samples to 4 in oriented samples) were investigated up to 12 months after implantation. Bioresorption of the samples was monitored using differential scanning calorimetry, scanning electron microscopy, and mechanical tests. Using the differential scanning calorimetry (DSC) method, it was shown that there is a gradual decrease in molecular weight due to a decrease in the temperatures of phase transitions and changes in peak shapes. It has also been shown that the addition of fillers containing water-soluble polymers accelerates the bioresorption of composite sutures. A thread made from pure PLA lost half its strength by the 9th month of implantation, whereas for threads with the addition of CNPEG or Poviargol, this happened after 3.5 months. This causes leaching of water-soluble agents and changes in the supramolecular structure of the filament. This study shows the promise of using these composite threads as a suture material.
Bing Song, Liang Wang, Jiawei Zhao, Yake Shen, Xiaoming Qian
Vol. 17., No.12., Pages 1257-1267, 2023
DOI: 10.3144/expresspolymlett.2023.95
Vol. 17., No.12., Pages 1257-1267, 2023
DOI: 10.3144/expresspolymlett.2023.95
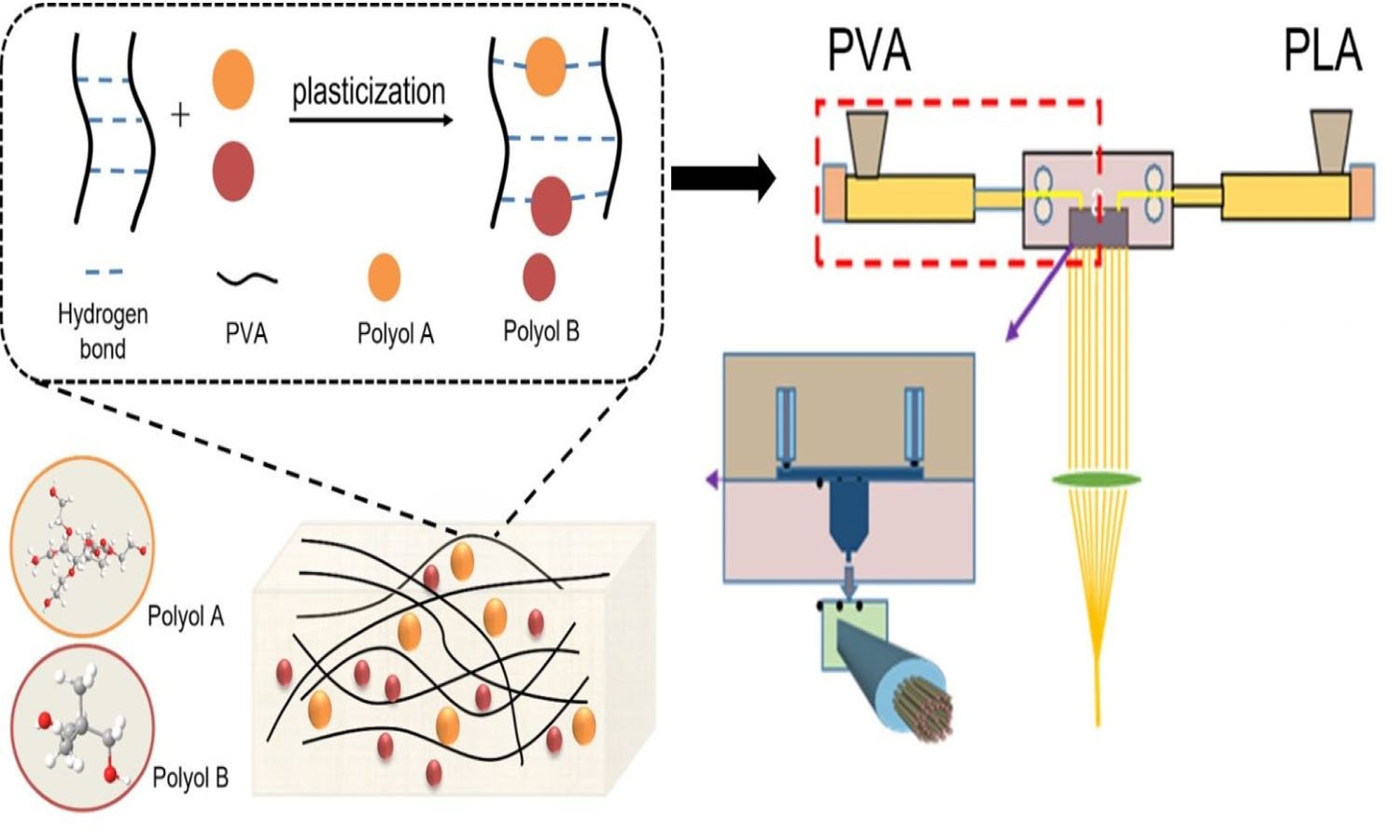
Polyvinyl alcohol (PVA) is a type of water-soluble polymer that is a candidate for ‘sea’ polymer to prepare seaisland fibers in industry. In this study, two types of polyols (sorbitol ether and neopentyl glycol) were mixed in different proportions and used to prepare thermoplastic PVA (TPVA) as a compound plasticizer. When the plasticizer was introduced, a blue shift occurred on the characteristic band of hydroxyl in the Fourier transform infrared spectroscopy (FTIR) pattern. The melting temperature (Tm) of the corresponding TPVA decreased, and their initial decomposition temperature (Td) increased to some degree. The addition of compound plasticizer made PVA show an improved Td up to 273.1 °C. Moreover, it led to an increment of the melting flow index and improved the resistance to oxidation at a temperature higher than 200°C. The increased spinnability enabled TPVA in PVA-PLA sea-island fiber making. PLA superfine fibers were obtained after splitting in water at 95 °C for just 3 min.