Simulation on pyrolysis behavior and reaction pathway of natural rubber and styrene-butadiene rubber by ReaxFF-MD
Xiaohua Li, Weiming Liu, Junlong Wang, Shanshan Shao, Weiliang Ding
Vol. 19., No.6., Pages 578-593, 2025
DOI: 10.3144/expresspolymlett.2025.44
DOI: 10.3144/expresspolymlett.2025.44
GRAPHICAL ABSTRACT
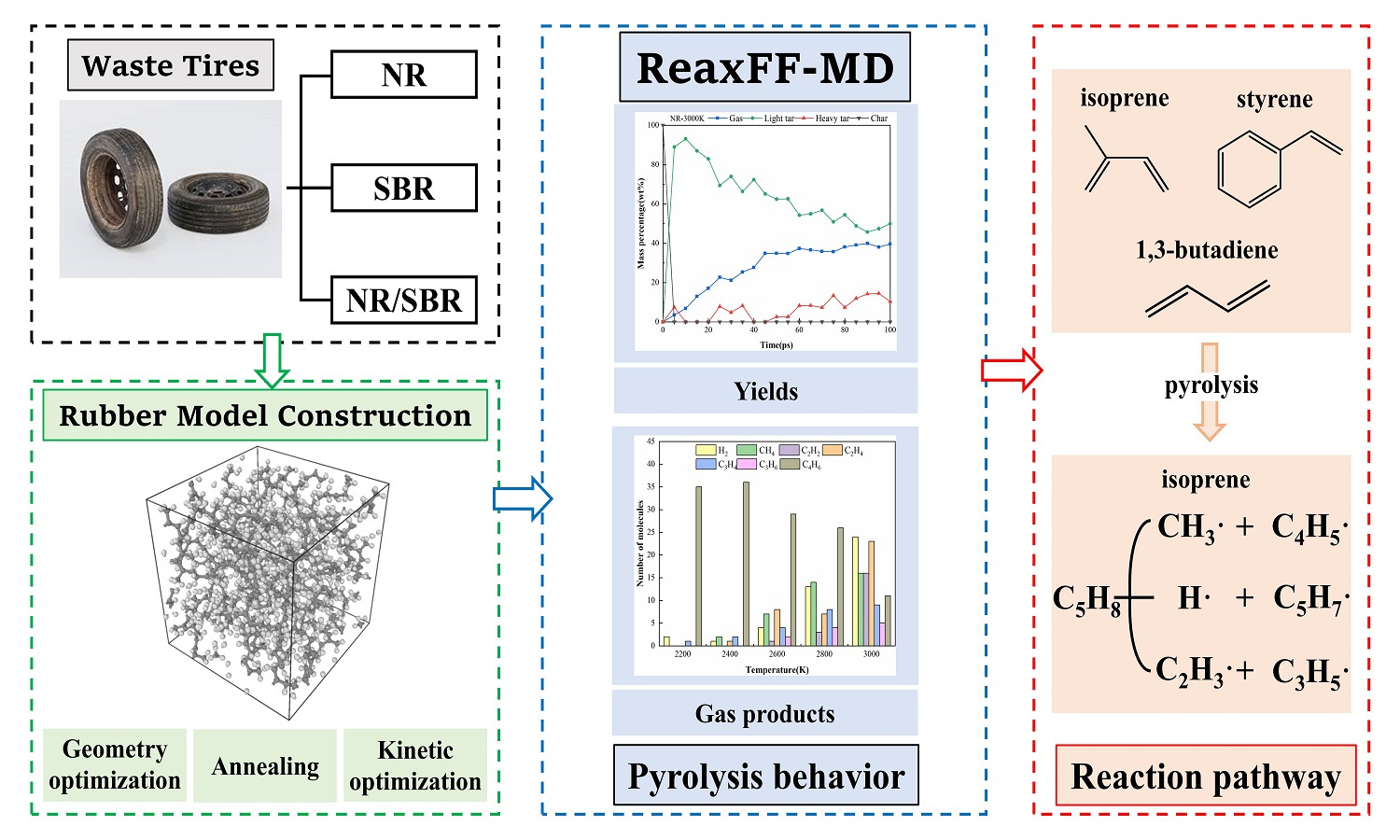
ABSTRACT
Pyrolysis is one of the effective methods for recycling waste tire rubber, and there are fewer studies on the simulation and mechanism of pyrolysis of multi-component mixed rubber. This study employs reactive force field molecular dynamics (ReaxFF-MD) simulations to analyze the pyrolysis product evolution processes of natural rubber (NR), styrene-butadiene rubber (SBR), and mixed rubber (NR/SBR). The results show that with increasing temperature, the gas yield of NR/SBR increases from 16.32% at 2000 K to 37.01% at 3000 K, and the molecular numbers of gas products such as H2 and small-molecule hydrocarbons increase with temperature. The co-pyrolysis of NR/SBR accelerates solid rubber pyrolysis time and promotes the formation of main gas products (excluding C4H6). Using simulation results, the reaction pathways of pyrolysis intermediates were analyzed: the main intermediates of NR are isoprene monomers and C10H16• short-chain radicals, while those of SBR are styrene and butadiene. The bond cleavage mechanisms of intermediates were compared through reaction energy barrier calculations. This study systematically reveals the pyrolysis product characteristics and reaction mechanisms of rubbers, providing theoretical support for the selective pyrolysis recycling of various waste rubbers.
RELATED ARTICLES
Zaheer ul Haq, Teng Ren, Xinyan Yue, Krzysztof Formela, Denis Rodrigue, Xavier Colom Fajula, Tony McNally, Dong Dawei, Yong Zhang, Shifeng Wang
Vol. 19., No.3., Pages 258-293, 2025
DOI: 10.3144/expresspolymlett.2025.20
Vol. 19., No.3., Pages 258-293, 2025
DOI: 10.3144/expresspolymlett.2025.20
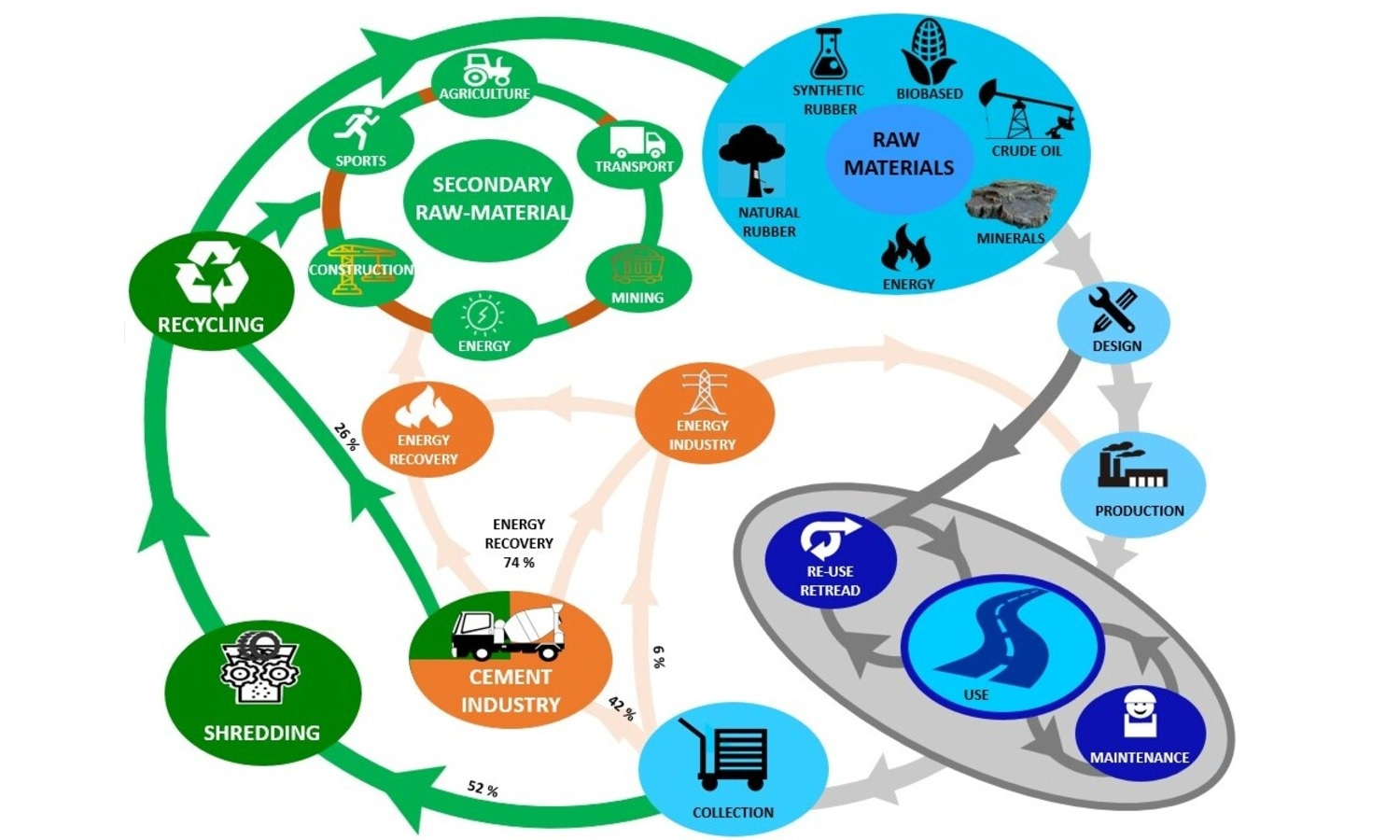
As a complex composite material, tire rubber has always presented significant environmental and waste management concerns due to its non-biodegradability and accumulation in landfills. The devulcanization of tire rubber has emerged as a historical challenge in the field of sustainable rubber engineering since Goodyear invented cross-linking in 1839. This review provides a comprehensive analysis of waste tire recycling processes, focusing on the sources, legislation, management strategies, and utilization across different regions. It explores the multifaceted challenges of devulcanizing rubber, with a specific focus on transitioning from ground tire rubber to the concept of multi-decrosslinking: sulfur bridge breakage, rubber chain depolymerization and micro-nano sized core-shell carbon black. Ideal devulcanization has restricted the release of reinforcing fillers, resulting in devulcanized rubber mainly containing dozens of micron particles, which hinder the wide usage of devulcanized rubber. This review comprehensively assesses the current state-of-the-art techniques for tire rubber devulcanization, including physical, chemical and biological methods. It explores the intricacies of ground tire rubber as a starting material, structural evolution of ground tire rubber during the devulcanization process and the associated challenges in achieving efficient devulcanization while retaining desirable mechanical properties. Furthermore, through an in-depth analysis of recent advancements, limitations and prospects, this paper offers a complete understanding of the challenges faced in tire rubber devulcanization. Considering the technical and environmental aspects of these processes, this work contributes to multi-decrosslinking, the ongoing discourse on sustainable materials development and circular economy initiatives, which pave the way for future innovations in the field of rubber recycling.
Markus Zach, Davide Tranchida, Enrico Carmeli, Jingbo Wang, Markus Gahleitner, Bernhard Hofko, Elena Pomakhina, Minna Aarnio-Winterhof
Vol. 18., No.7., Pages 715-727, 2024
DOI: 10.3144/expresspolymlett.2024.53
Vol. 18., No.7., Pages 715-727, 2024
DOI: 10.3144/expresspolymlett.2024.53
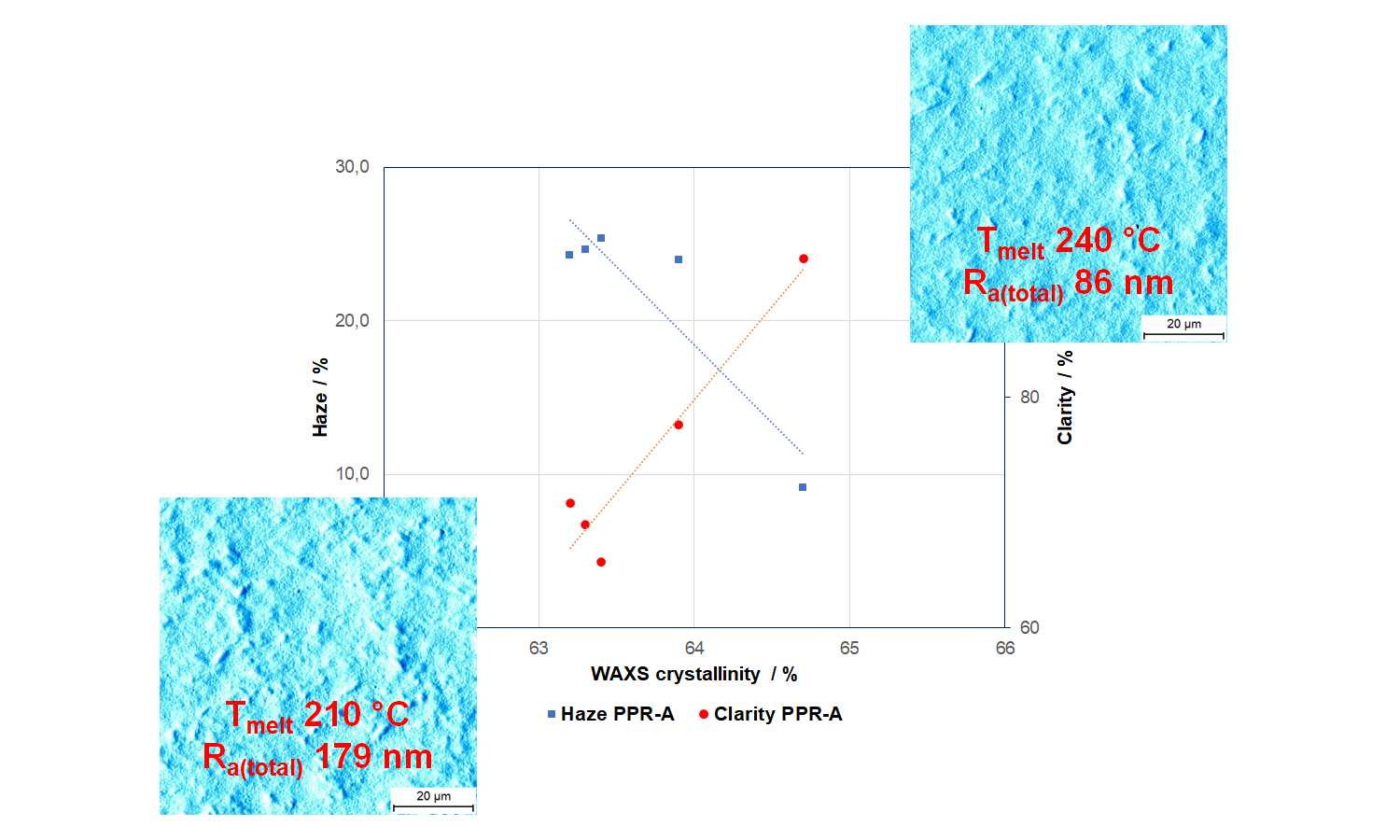
Blown films from ethylene-propylene random copolymers (C2C3-RACOs) are used in many packaging applications today, constituting a major fraction of both mono- and multilayer packaging film constructions. Combining high processing speed and output with good mechanical and optical performance, mostly high toughness and low haze, requires understanding the structure-property-processing relations. To improve said understanding for C2C3-RACO blown films, two commercial grades with a nearly identical C2 content of ~4.4 wt% and identical melt flow rate (MFR) but different nucleation were selected. These were tested in a processing study, varying melt temperature, blow-up ratio (BUR) and neck length. The film structure was analysed by wide angle X-ray scattering (WAXS) and atomic force microscopy (AFM), and the performance by standard mechanical and optical tests. Variation of film crystallinity was found to be in the range of 62 to 65%, much smaller than in earlier cast film studies on comparable polymers. The tensile modulus is the only performance parameter for which a general positive correlation to crystallinity can be found, blown films being about 50% stiffer than the softest cast films of a comparable polymer. Ductility and toughness are enhanced by higher orientation, resulting from higher BUR and/or higher neck length. For transparency and haze, low surface roughness is decisive at comparable crystallinity, which can be achieved by increasing melt temperature.