Influence of epoxide content and blend ratios on strength and damping properties of thermoplastic vulcanizates based on epoxidized natural rubber and poly(ether-block-amide) copolymer blends
Azizon Kaesaman, Rawviyanee Romin, Charoen Nakason
Vol. 17., No.10., Pages 1056-1069, 2023
DOI: 10.3144/expresspolymlett.2023.79
DOI: 10.3144/expresspolymlett.2023.79
GRAPHICAL ABSTRACT
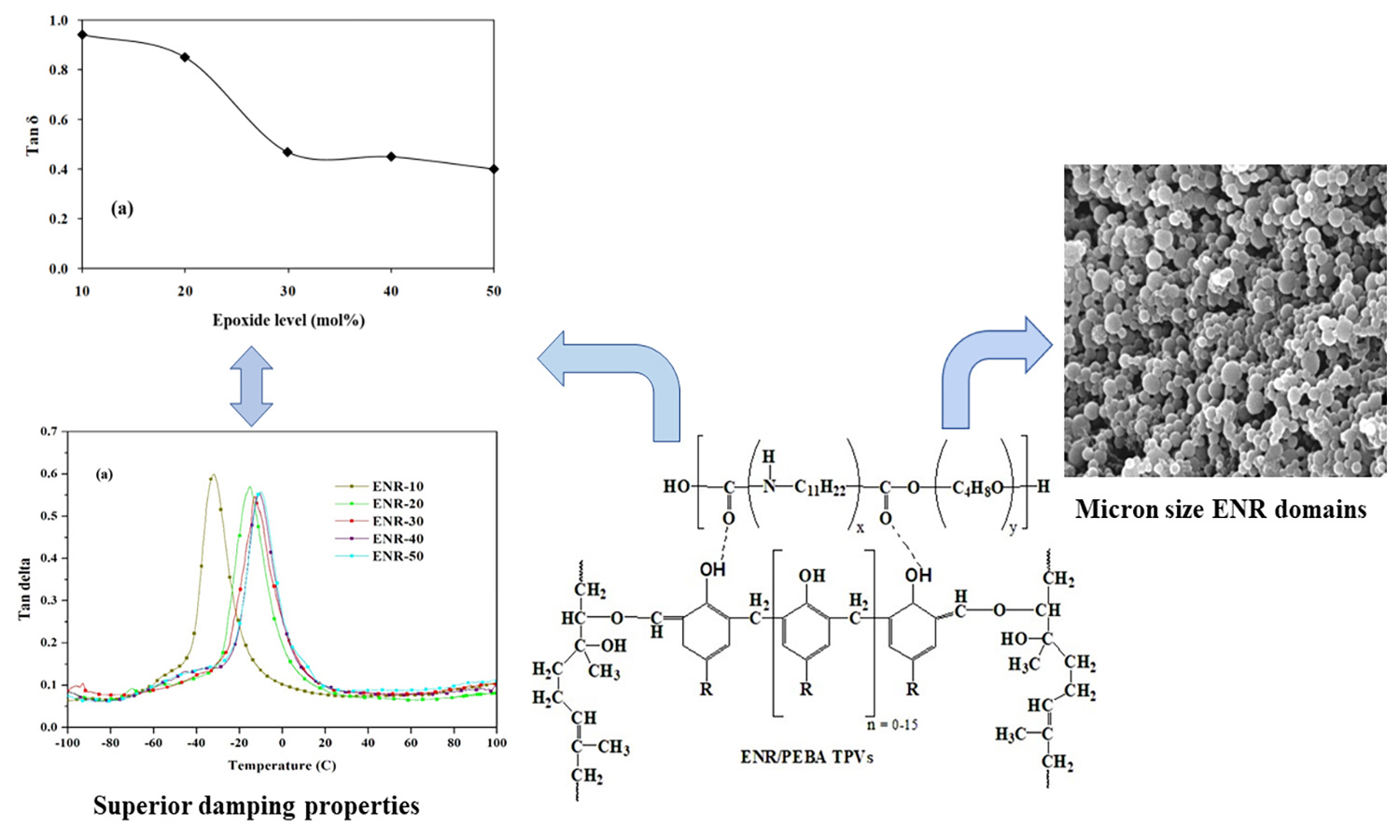
ABSTRACT
Epoxidized natural rubber (ENR) with varying levels of epoxide groups ranging from 10 to 50 mol% was prepared and dynamically phenolic vulcanized by blending it with poly(ether-block-amide) copolymer (PEBA). The results indicate that the thermoplastic vulcanizates (TPVs) of ENR/PEBA blends display a sea-island morphology and enhance a number of properties. Specifically, increasing the epoxide content and PEBA proportion enhances strength properties, including higher Young’s modulus (stiffness), toughness, tensile properties, and hardness, along with smaller vulcanized ENR domains dispersed in the PEBA matrix. Moreover, the decrease in tension set values indicates an improvement in the elastic properties. The attributed cause of this is the interaction between the polar groups present in the phenolic-cured ENR domains and the PEBA molecules. As a result, interfacial adhesion between the ENR domains and PEBA interfaces improved, contributing to the observed enhancements in the strength and elastic properties of the TPVs with smaller ENR domains. Furthermore, an increase in the epoxide content was found to be correlated with a decrease in tanδ and tension set, which further supported the observed improvements in strength and elasticity. Additionally, the ENR/PEBA blends showed a single glass transition temperature (Tg), while pure PEBA exhibited two Tgs. The presence of a single Tg in the ENR/PEBA blend is attributed to the overlapping of the Tg of the ENR and PEBA immiscible blend components.
RELATED ARTICLES
Kriengsak Damampai, Kanoknan Boonpan, Yeampon Nakaramontri
Vol. 19., No.4., Pages 409-422, 2025
DOI: 10.3144/expresspolymlett.2025.30
Vol. 19., No.4., Pages 409-422, 2025
DOI: 10.3144/expresspolymlett.2025.30
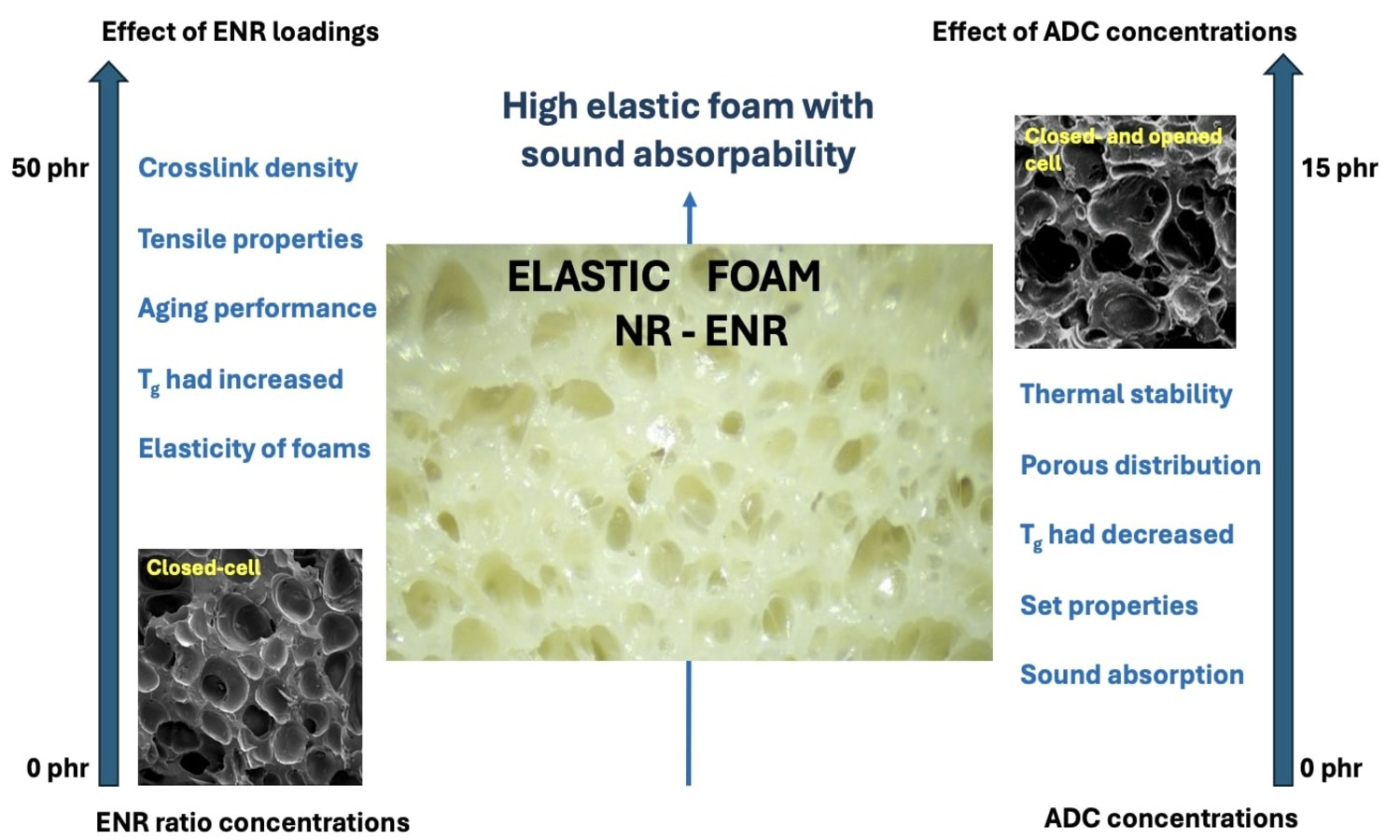
This study investigated the properties of the natural rubber (NR) foam filled with azodicarbonamide (ADC) blowing agents by combination to various ratios of epoxidized NR (ENR) for flexible foam applications. Compound operation was prepared with an open two-roll mill and the production was fabricated by compression molding. The study elucidated properties related to crosslinking behaviors, mechanical and dynamic properties, elasticity, abrasion, weathering resistance, and sound absorption efficiency. The ENR and ADC concentrations affected the tensile testing and also the durability properties of the NR/ENR. The NR and ENR foam of 60/40 filled with 10 phr of ADC demonstrated good properties across various parameters, showing acceptable tensile properties, abrasion resistance, and QVA light resistance. Additionally, the presence of a closed-cell structure in the blends reduced crack propagation in the NR matrix during aging, improving weathering resistance. The absorption coefficient increased with higher ADC content, being optimal at 15 phr, due to the lower density and higher porosity of the opened-cell material, which enhances its ability to interact more effectively with incoming energy at 1600 and 6400 Hz. The findings encourage the use of ENR for blending in NR for improved ENR and ADC concentrations since dipole-dipole interaction from ENR-ADC caused ADC dispersability, providing complexed foam structures for force expansion and aslo sound wave absorption.
Nabil Hayeemasae, Sitisaiyidah Saiwari, Siriwat Soontaranon, Mohamad Irfan Fathurrohman, Abdulhakim Masa
Vol. 19., No.3., Pages 339-349, 2025
DOI: 10.3144/expresspolymlett.2025.24
Vol. 19., No.3., Pages 339-349, 2025
DOI: 10.3144/expresspolymlett.2025.24
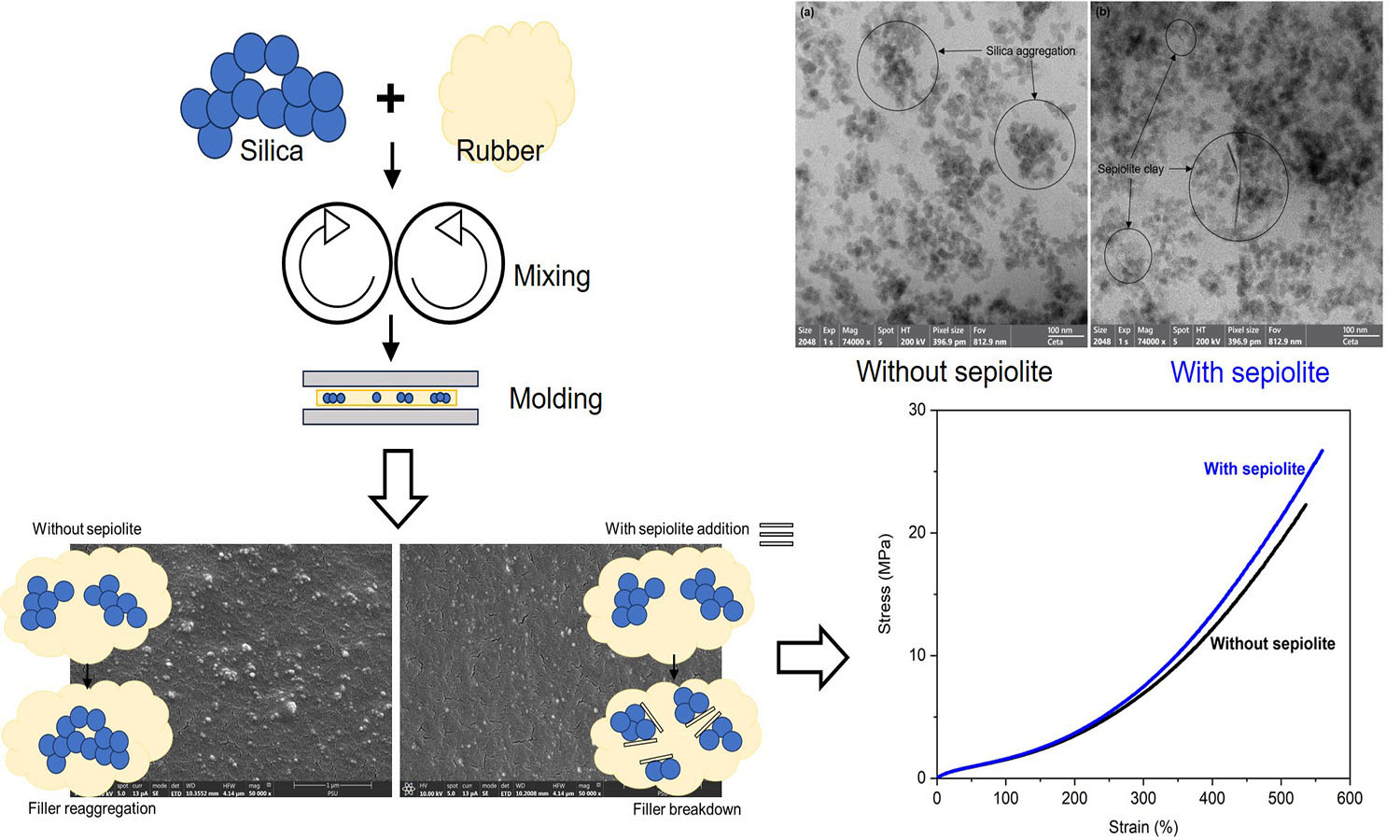
Natural rubber (NR) composites filled with silica and crosslinked with phenolic resin were prepared in this study. The influence of a small sepiolite addition (1–5 part(s) per hundred parts of rubber, phr) on the properties of NR composites was studied. It was found that sepiolite reduced silica aggregate size, allowing improved dispersion in the NR matrix. Sepiolite facilitates silica dispersion by locating at the silica surfaces and acting as a barrier that prevents agglomeration of silica filler. The swelling resistance, crosslink density, tensile strength, and strain-induced crystallization were all strengthened by incorporating sepiolite because of the improved silica dispersion. The greatest tensile strength was achieved at a 2 phr sepiolite addition level. The improvement was about 18% over the reference composite due to the greatest filler-rubber interactions and the finest filler dispersion. The results clearly indicate that sepiolite clay can be applied as a dispersing agent in silica-containing rubber composites.
Marek Pöschl, Radek Stoček, Petr Zádrapa, Martin Stěnička, Gert Heinrich
Vol. 18., No.12., Pages 1178-1190, 2024
DOI: 10.3144/expresspolymlett.2024.90
Vol. 18., No.12., Pages 1178-1190, 2024
DOI: 10.3144/expresspolymlett.2024.90
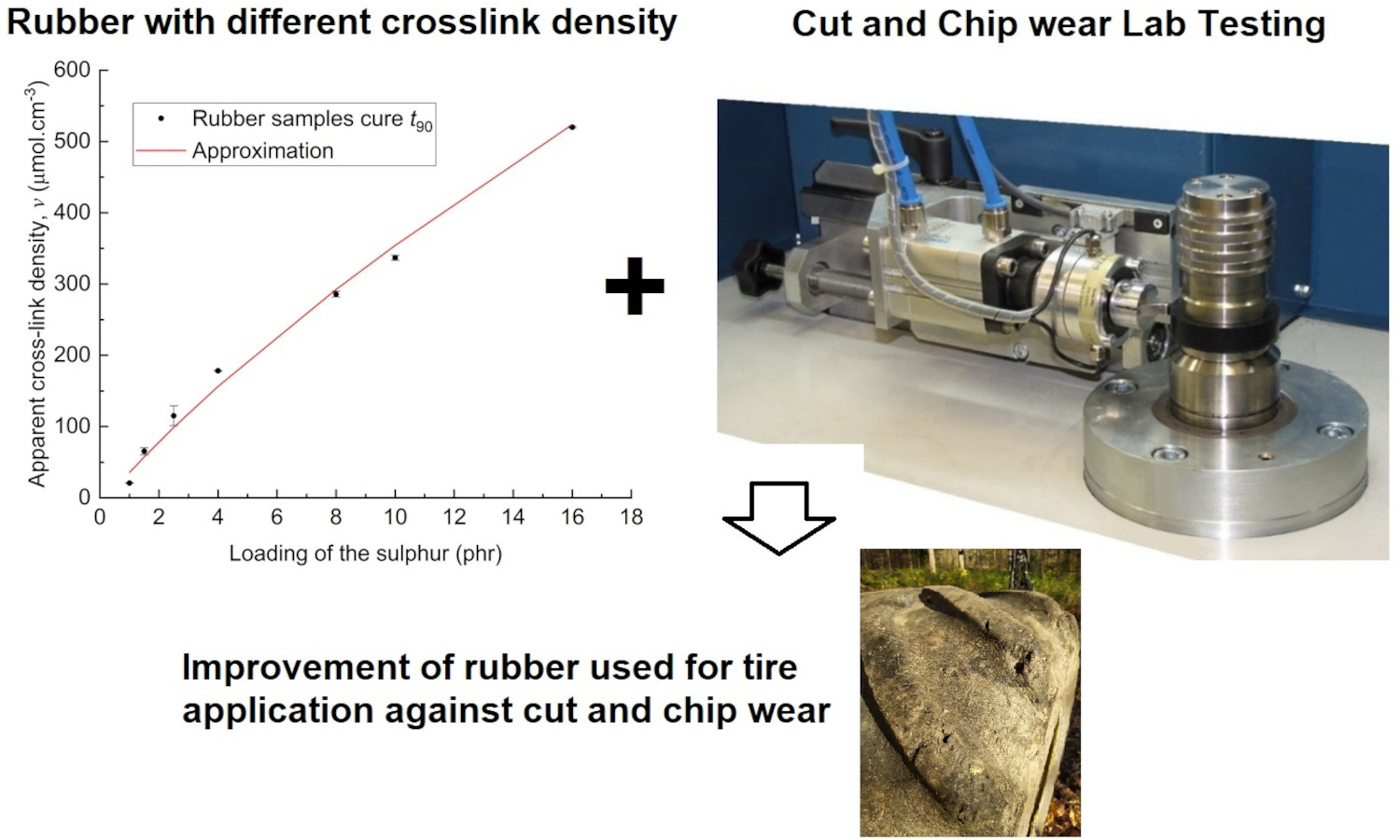
This paper extends previous studies by the authors that aimed to describe the effect of apparent cross-link density (CLD) of the rubber polymer networks on the fracture mechanism caused by cut and chip (CC) wear of natural rubber (NR), demonstrating the positive effect of conventional vulcanization (CV). This work is focused on the determination of the effect of CLD while keeping constant the accelerator-to-sulfur ratio A/S = 0.2, typical for CV systems. For this ratio, different sulfur quantities were chosen, and the concentration of the accelerator N-tert-butyl-benzothiazole sulphonamide (TBBS) was calculated to achieve CLDs in a range from 35 to 524 μmol・cm–3. Standard analyses such as tensile tests, hardness, rebound resilience and DIN abrasion were performed. From these analyses, the optimum physical properties of the NR-based rubber were estimated to be in the CLD range of approximately 60 to 160 μmol・cm–3. A CC wear analysis was performed with an Instrumented cut and chip analyzer (ICCA) and it was found that the highest CC wear resistance of the NR is in the CLD range of 35 to 100 μmol・cm–3. Furthermore, the effect of straininduced crystallization (SIC) of NR on CC wear and its dependence on the CLD region was discussed. For the first time, we determine a CLD range for a CV system in which the material achieves both optimal mechanical properties and CC wear resistance.
Kamonthip Rittimas, Skulrat Pichaiyut, Charoen Nakason
Vol. 18., No.11., Pages 1149-1163, 2024
DOI: 10.3144/expresspolymlett.2024.87
Vol. 18., No.11., Pages 1149-1163, 2024
DOI: 10.3144/expresspolymlett.2024.87
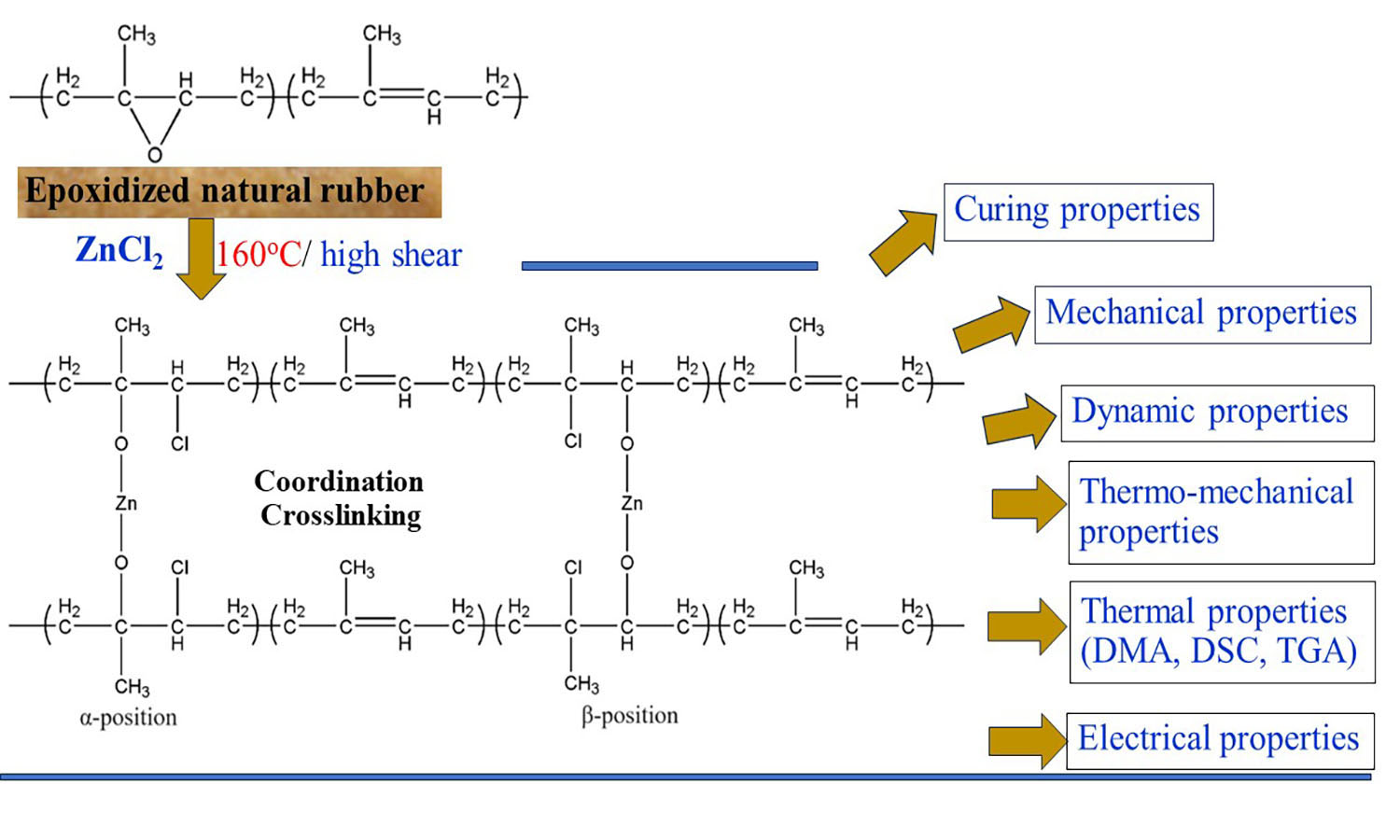
Epoxidized natural rubber with 50 mol% epoxide (ENR-50) was compounded with zinc chloride (ZnCl2) and subjected to torque response analysis using a moving die rheometer. It was found that different ZnCl2 concentrations (3, 5, 7, 9, and 12 millimoles (mmol)) mixed in ENR-50 exhibited positive torque responses, prompting further molecular characterization using Fourier transform infrared spectroscopy. The results indicated distinct absorption peaks at wavenumbers of 442 and 809 cm–1, which signify the presence of –O–Zn–O– coordination linkages. The curing characteristics of ENR and ZnCl2 compounds showed that increasing ZnCl2 content resulted in higher minimum and maximum torque values, but also led to a decrease in scorch time and cure rate index (CRI). Moreover, higher ZnCl2 concentrations enhanced the strength properties (tensile strength, moduli, stiffness, toughness, and hardness), crosslink densities, dynamic shear moduli, initial modulus during relaxation experiments, and thermal resistance, as evidenced by temperature scanning stress relaxation (TSSR), thermogravimetric analysis, and dynamic mechanical analysis. However, an increase in ZnCl2 content led to a reduction in elongation at break due to the higher crosslink density within the coordination networks in the ENR matrix, which resulted in the movement constraint of the rubber vulcanizate.
Rattanawadee Ninjan, Bencha Thongnuanchan, Natinee Lopattananon, Subhan Salaeh, Phakawat Thongnuanchan, Pornsuwan Buangam
Vol. 18., No.11., Pages 1077-1093, 2024
DOI: 10.3144/expresspolymlett.2024.83
Vol. 18., No.11., Pages 1077-1093, 2024
DOI: 10.3144/expresspolymlett.2024.83
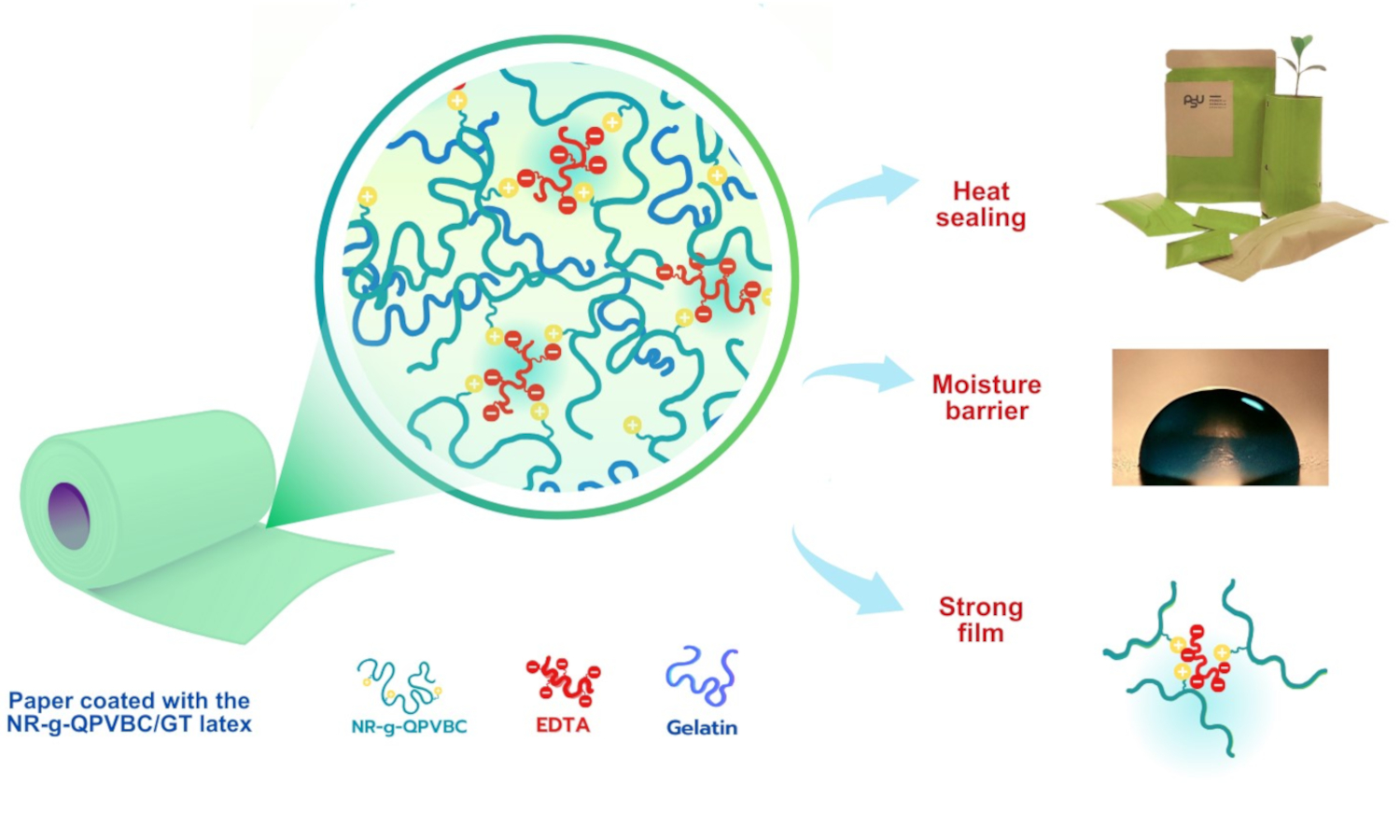
Research into sustainable packaging materials has gained increasing importance due to the pressing environmental concerns related to plastic waste. The present study focused on developing a sustainable paper coating based on modified natural rubber (NR) latex filled with gelatin (GT). The graft copolymer latex of NR and poly(vinylbenzyl chloride) bearing quaternary ammonium groups, abbreviated as NR-g-QPVBC, was first synthesized. GT was then incorporated into the latex, and the combination of these materials resulted in a heat-sealable film with good tensile properties and a water barrier. The ionic crosslinking of the latex film was achieved by the reaction with ethylenediaminetetraacetic acid (EDTA). Heat-sealing studies of the NR-g-QPVBC latex film filled with GT (NR-g-QPVBC/GT) revealed its heat-sealability at 160 °C. Scanning electron microscope (SEM) analysis further confirmed the diffusion of the chains across the interface during heat sealing. Dip coating was a method for depositing latex film on kraft paper. The paper coated with the NR-g-QPVBC/GT latex showed a significant increase in dry and wet-tensile strength compared to the uncoated paper. The sealing process was optimized to achieve a heat-seal strength of 755.31 N/m at a dwell time of 3 s and a temperature of 160 °C. The research's practical application was demonstrated by transforming the coated paper into various heat-sealable bags using a handheld bag sealer.