In-situ formation of ZnO anchored silica: Sustainable replacement of conventional ZnO in SBR/NR blends
Vol. 17., No.12., Pages 1268-1285, 2023
DOI: 10.3144/expresspolymlett.2023.96
DOI: 10.3144/expresspolymlett.2023.96
GRAPHICAL ABSTRACT

ABSTRACT
The global concern over zinc leaching into aquatic ecosystems has led researchers to seek ways to reduce zinc oxide (ZnO) content in rubber products. Conventional microsized ZnO, commonly used in the rubber industry, poses dispersion challenges due to its hydrophilic nature and micron size within the hydrophobic rubber matrix. Therefore, higher amounts of ZnO are added, elevating the risk to aquatic life. A promising alternative involves using highly dispersible ZnO with active zinc (Zn) centers instead of conventional ZnO. Another approach includes incorporating ZnO-anchored silica particles into the rubber matrix, which requires additional ex-situ fabrication. This study presents an innovative method where ZnO-anchored silica is generated in situ during the blending of styrene-butadiene rubber/natural rubber (SBR/NR). The study also evaluates the effectiveness of active, nano-sized, and octylamine-modified ZnO as activators compared to conventional ZnO, by introducing silica filler, octylamine-modified and high surface area ZnO anchor onto the silica surface, forming Si–O–Zn covalent bonds. This protective layer reduces filler aggregation and the Payne effect. Even with 60% less usage, these activators in the SBR/NR blend significantly enhance tensile strength (31.27%) and elongation at break (49.13%) compared to conventional ZnO. These results point towards the possibility of a cost-effective and sustainable replacement for conventional ZnO.
RELATED ARTICLES
Sirithorn Kaewklum, Parisa Faibunchan, Apinya Krainoi, Banyat Cherdchim, Jutharat Intapun
Vol. 19., No.9., Pages 929-945, 2025
DOI: 10.3144/expresspolymlett.2025.70
Vol. 19., No.9., Pages 929-945, 2025
DOI: 10.3144/expresspolymlett.2025.70
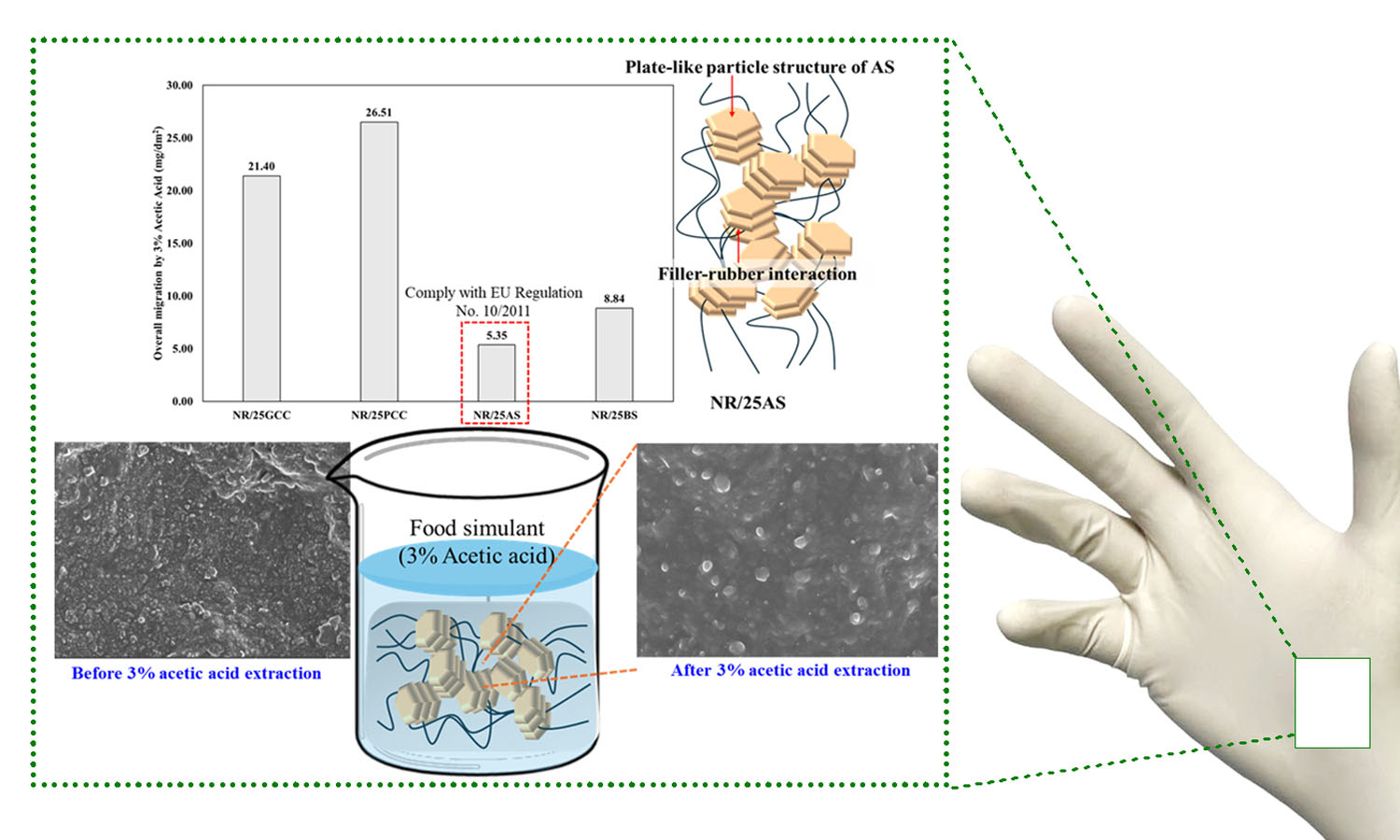
Powder-free natural rubber gloves for chemical migration resistance of food-contact grade are prepared using a variety of fillers, including ground calcium carbonate (GCC), precipitated calcium carbonate (PCC), aluminum silicate (AS), and barium sulfate (BS)-filled natural rubber (NR), respectively. The properties of NR gloves, including mechanical, dynamic mechanical, and thermal properties, were investigated. Furthermore, the overall migration test of NR gloves was conducted according to the regulations for food contact gloves (EU Regulation No. 10/2011), using 3% acetic acid as the simulant. Among the fillers studied, the plate-like particles of AS facilitated the most effective filler-rubber interactions and reinforcement in AS-filled natural rubber (NR/AS). Consequently, the highest crosslink density, force at break, and damping properties of NR gloves were achieved by applying AS in the NR matrix. Moreover, the lowest overall migration level was observed for NR/AS with a value of 5.35 mg/dm2, which complies with EU Regulation (overall migration of food simulants shall not exceed 10 mg/dm2). Therefore, NR gloves filled with AS are suitable for food-contacting NR gloves.
Jose James, George Vazhathara Thomas, Sisanth Krishnageham Sidharathan, Mohammad Arif Poothanari, Sabu Thomas
Vol. 19., No.7., Pages 697-705, 2025
DOI: 10.3144/expresspolymlett.2025.53
Vol. 19., No.7., Pages 697-705, 2025
DOI: 10.3144/expresspolymlett.2025.53
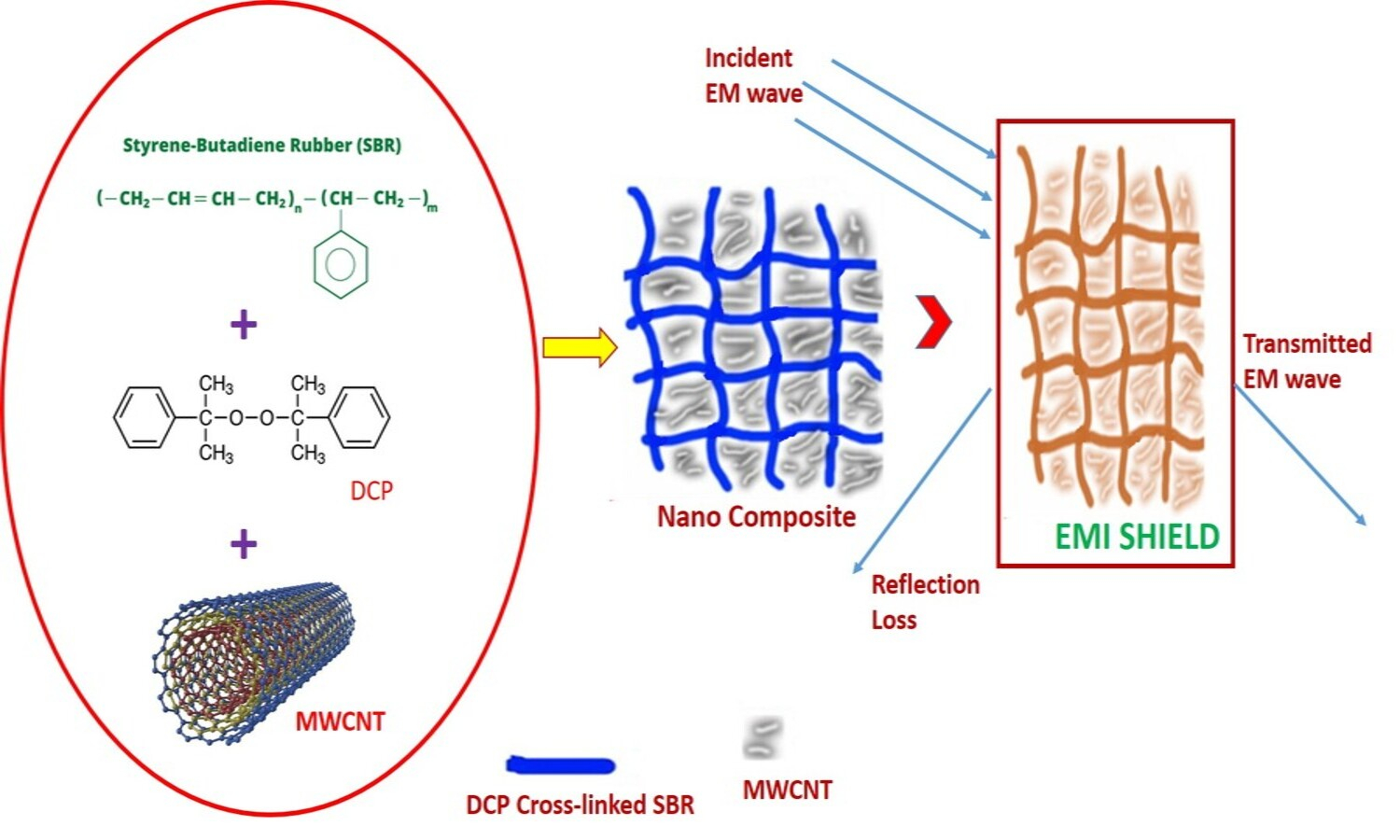
A nanocomposite of styrene butadiene rubber (SBR) and multi-walled carbon nanotubes (MWCNT) was fabricated using an internal melt mixer. Systematically investigated the role of MWCNT loading on the mechanical, dielectric, electrical and Electromagnetic interference (EMI) shielding characteristics of developed nanocomposites. The fine dispersion of MWCNTs in the SBR matrix was clearly observed from high-resolution transmission electron microscope images. The nanocomposites exhibited outstanding electrical, dielectric and EMI shielding behaviours (~45 dB at 20 phr of MWCNT). A high conductivity of 0.92 S/cm was attained in the nanocomposites and is attributable to the establishment of percolation networks of MWCNT in the SBR matrix. These composites displayed reasonably good mechanical properties because of the reinforcing effect of MWCNT. The economically viable and easy fabrication protocol of this nanocomposite can act as a platform for the synthesis of low-cost and highly effective composite for EMI shielding applications.
Nabil Hayeemasae, Sitisaiyidah Saiwari, Siriwat Soontaranon, Mohamad Irfan Fathurrohman, Abdulhakim Masa
Vol. 19., No.3., Pages 339-349, 2025
DOI: 10.3144/expresspolymlett.2025.24
Vol. 19., No.3., Pages 339-349, 2025
DOI: 10.3144/expresspolymlett.2025.24
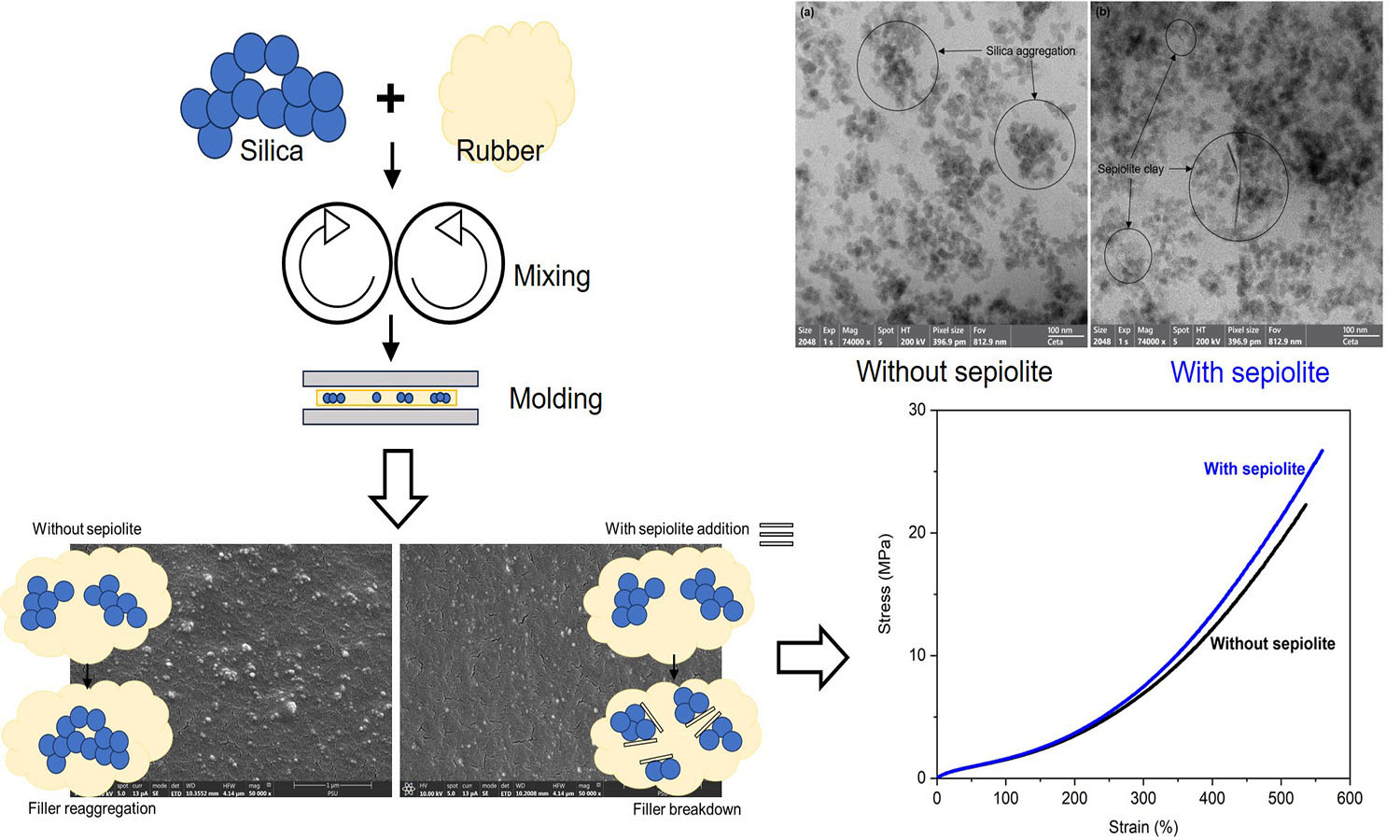
Natural rubber (NR) composites filled with silica and crosslinked with phenolic resin were prepared in this study. The influence of a small sepiolite addition (1–5 part(s) per hundred parts of rubber, phr) on the properties of NR composites was studied. It was found that sepiolite reduced silica aggregate size, allowing improved dispersion in the NR matrix. Sepiolite facilitates silica dispersion by locating at the silica surfaces and acting as a barrier that prevents agglomeration of silica filler. The swelling resistance, crosslink density, tensile strength, and strain-induced crystallization were all strengthened by incorporating sepiolite because of the improved silica dispersion. The greatest tensile strength was achieved at a 2 phr sepiolite addition level. The improvement was about 18% over the reference composite due to the greatest filler-rubber interactions and the finest filler dispersion. The results clearly indicate that sepiolite clay can be applied as a dispersing agent in silica-containing rubber composites.
Marek Pöschl, Radek Stoček, Petr Zádrapa, Martin Stěnička, Gert Heinrich
Vol. 18., No.12., Pages 1178-1190, 2024
DOI: 10.3144/expresspolymlett.2024.90
Vol. 18., No.12., Pages 1178-1190, 2024
DOI: 10.3144/expresspolymlett.2024.90
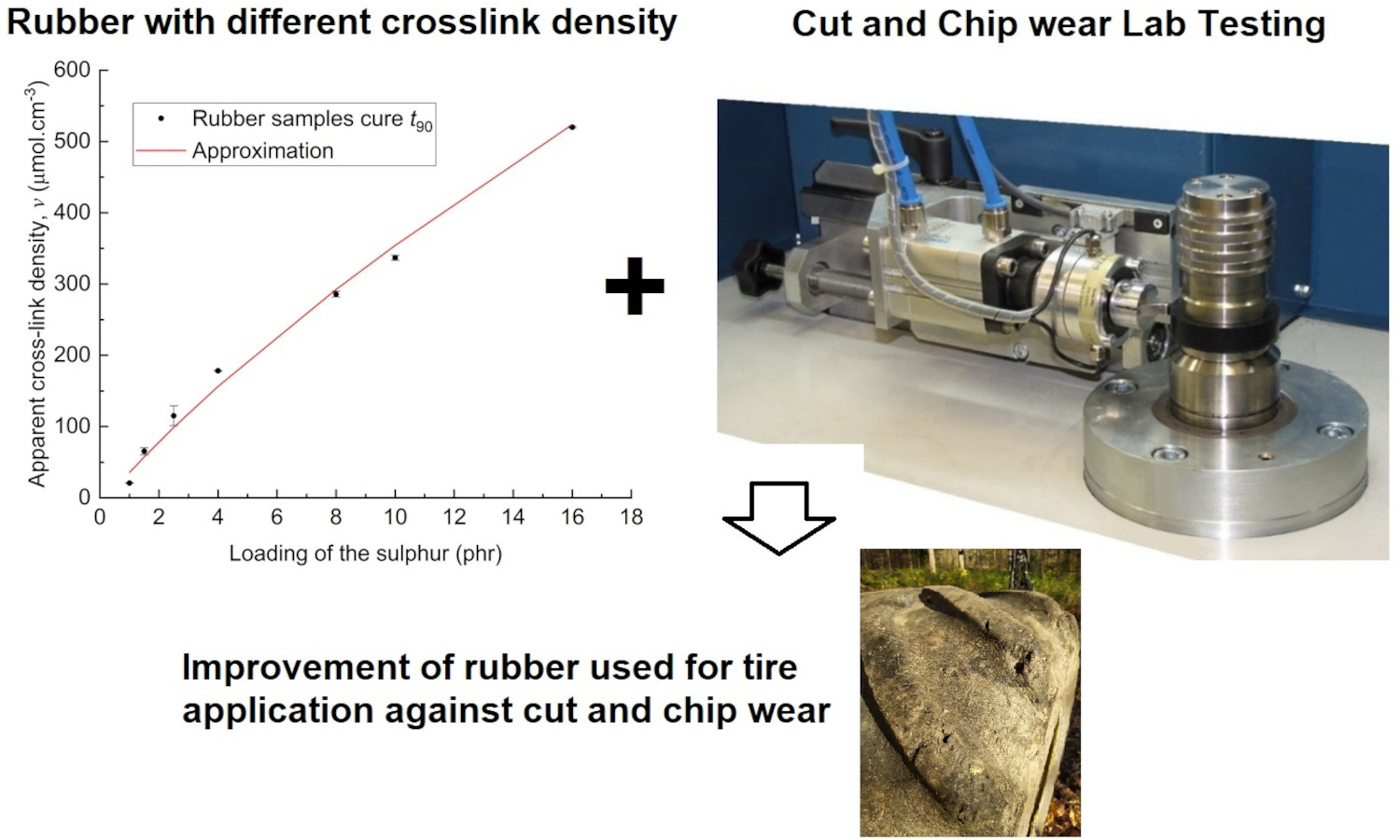
This paper extends previous studies by the authors that aimed to describe the effect of apparent cross-link density (CLD) of the rubber polymer networks on the fracture mechanism caused by cut and chip (CC) wear of natural rubber (NR), demonstrating the positive effect of conventional vulcanization (CV). This work is focused on the determination of the effect of CLD while keeping constant the accelerator-to-sulfur ratio A/S = 0.2, typical for CV systems. For this ratio, different sulfur quantities were chosen, and the concentration of the accelerator N-tert-butyl-benzothiazole sulphonamide (TBBS) was calculated to achieve CLDs in a range from 35 to 524 μmol・cm–3. Standard analyses such as tensile tests, hardness, rebound resilience and DIN abrasion were performed. From these analyses, the optimum physical properties of the NR-based rubber were estimated to be in the CLD range of approximately 60 to 160 μmol・cm–3. A CC wear analysis was performed with an Instrumented cut and chip analyzer (ICCA) and it was found that the highest CC wear resistance of the NR is in the CLD range of 35 to 100 μmol・cm–3. Furthermore, the effect of straininduced crystallization (SIC) of NR on CC wear and its dependence on the CLD region was discussed. For the first time, we determine a CLD range for a CV system in which the material achieves both optimal mechanical properties and CC wear resistance.
Agata Rodak, Józef Haponiuk, Shifeng Wang, Krzysztof Formela
Vol. 18., No.12., Pages 1191-1208, 2024
DOI: 10.3144/expresspolymlett.2024.91
Vol. 18., No.12., Pages 1191-1208, 2024
DOI: 10.3144/expresspolymlett.2024.91
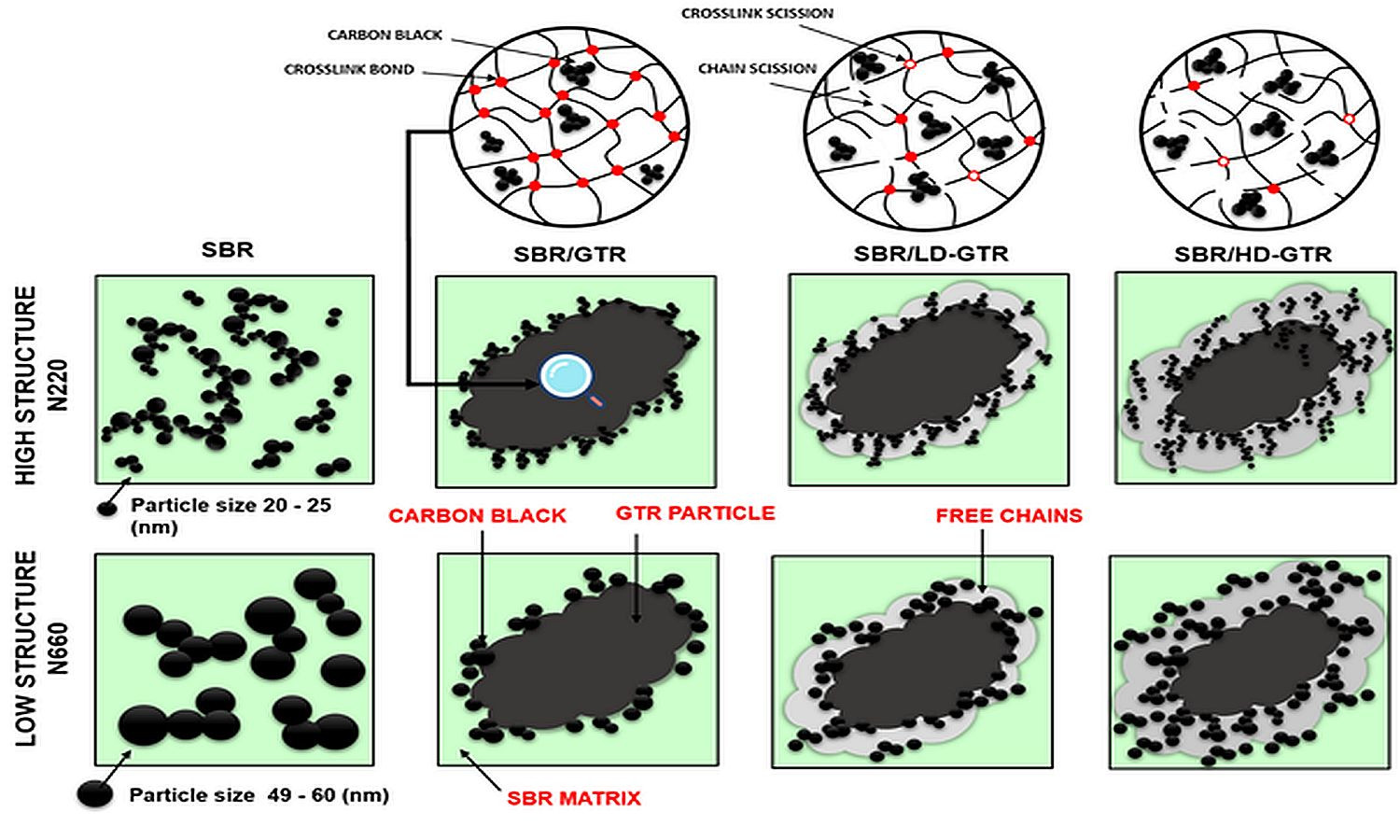
Carbon black migration between ground tire rubber (GTR) and rubber matrix is essential in developing high-performance rubber/GTR composites. In this work, carbon black N220 (surface area: 107.1 m2/g, particle size: 20–25 nm) and N660 (surface area: 33.1 m2/g, particle size: 49–60 nm) were used as the reinforcement fillers for styrene-butadiene rubber (SBR) blended with reclaimed GTR. The combined effects of GTR devulcanization level and carbon black grade on the properties of SBR/GTR composites were investigated considering curing characteristics, thermal stability, physico-mechanical properties, dynamic mechanical properties, swelling behavior, and morphology. The results showed that, regardless of GTR devulcanization level and carbon black grade, application of GTR resulted in deterioration of mechanical properties compared to a reference sample without GTR. It was observed the reinforcement effect of carbon black in SBR/GTR composites was more visible with higher devulcanization level of GTR and lower particle sizes of carbon black fillers. SBR/GTR composites reinforced with carbon black N220 were characterized by tensile strength in the range of 15.3–16.3 MPa and abrasion resistance in the range of 120–123 mm3, which justify their potential application in the manufacturing of technical rubber goods or footwear.