Content
All issues / Volume 19 (2025) / Issue 3 (March)
József Gábor Kovács, Tibor Czigány
Vol. 19., No.3., Pages 230-232, 2025
DOI: 10.3144/expresspolymlett.2025.17
Vol. 19., No.3., Pages 230-232, 2025
DOI: 10.3144/expresspolymlett.2025.17
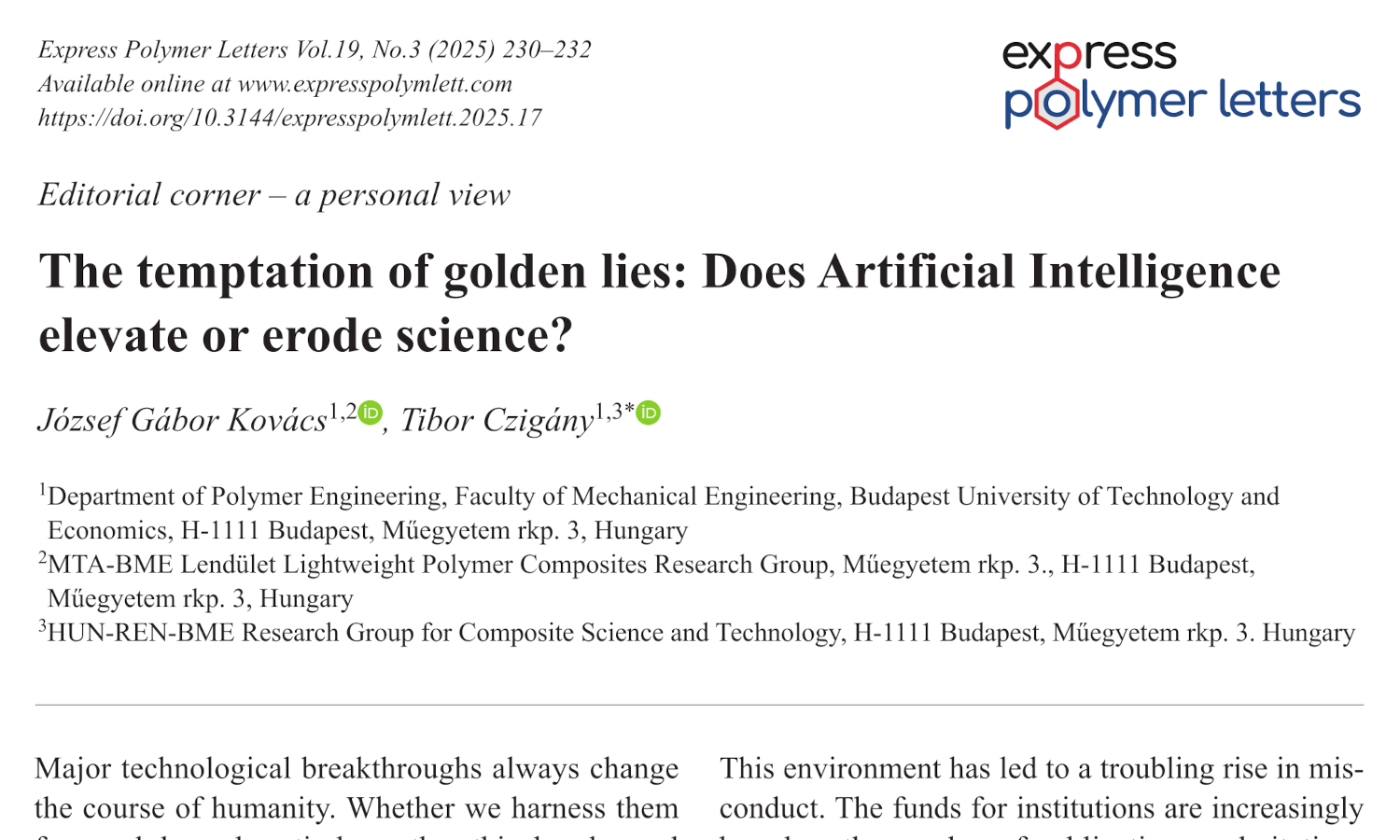
This is an editorial article. It has no abstract.
Delia Mihaela Raţă, Anca Niculina Cadinoiu, Luiza Mădălina Grădinaru, Paul Codrin Fuioaga, Gabriela Vochita, Christelle Delaite, Leonard Ionuţ Atanase
Vol. 19., No.3., Pages 233-245, 2025
DOI: 10.3144/expresspolymlett.2025.18
Vol. 19., No.3., Pages 233-245, 2025
DOI: 10.3144/expresspolymlett.2025.18
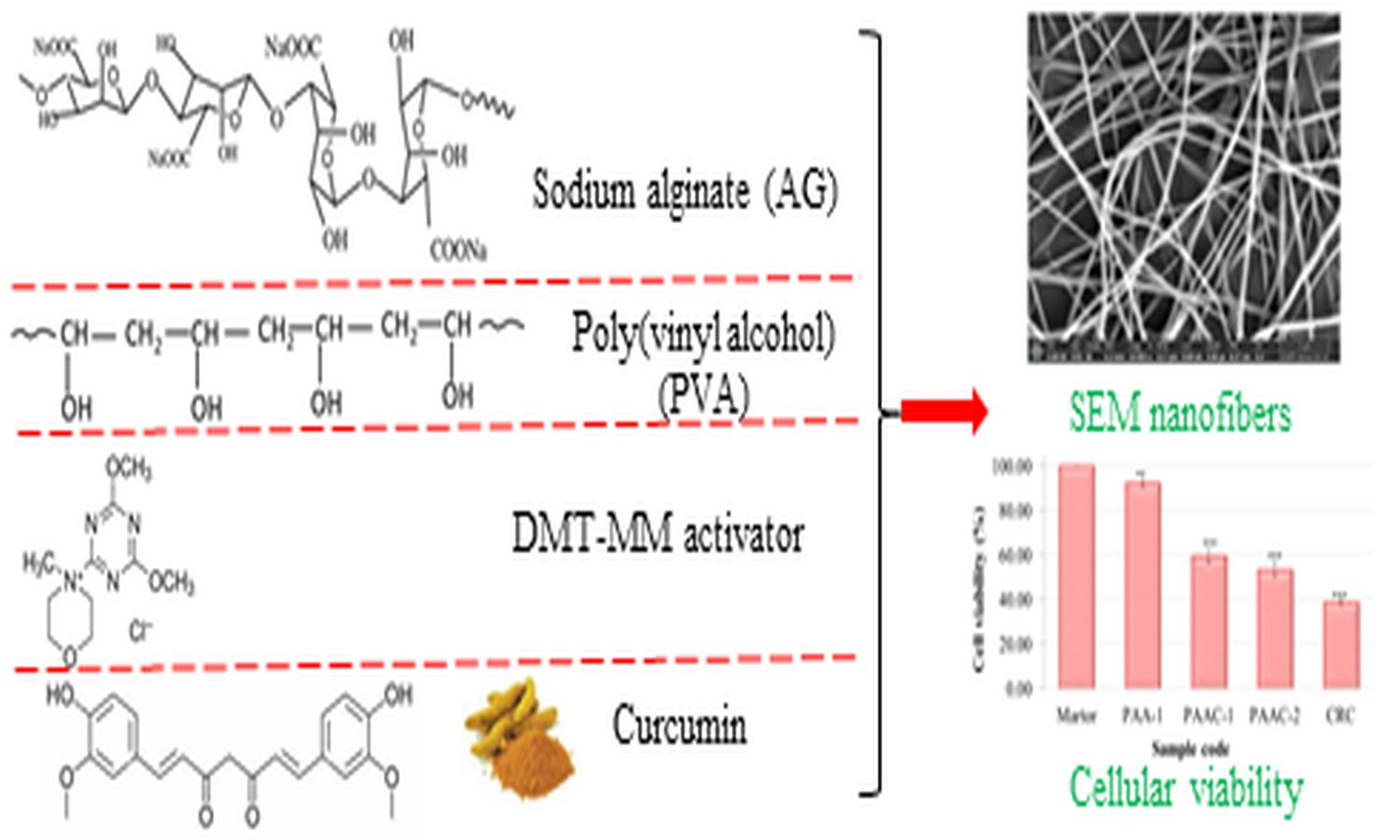
Curcumin (CRC) is a natural active principle with important anti-inflammatory, antioxidant, antibacterial, and antitumor properties but has some limitations, such as poor bioavailability, low water solubility, and rapid metabolism. To preserve CRC’s benefits and eliminate its limitations, novel CRC-loaded core-shell electrospun nanofibers were designed. The nanofibers were prepared by co-axial electrospinning method using poly(vinyl alcohol)/CRC as core and poly(vinyl alcohol)/sodium alginate as shell. Polymer coating protects the CRC, increasing its stability. The swelling degree of CRCloaded nanofibers at pH 5.4 was around 326% higher than at pH 7.4 (297%) due to the repulsions of the anion-anion COO–groups. The release efficiency of CRC at pH 7.4 was 81%, while at pH 5.4 was about 96%. In the first 6 h, there was a slower release of CRC from the nanofibers in both acidic and slightly alkaline environments. Nanofibers showed good hemocompatibility, the values being between 2.36–3.22% after the first 90 min of contact, and after 180 min of treatment, the degree of erythrocyte lysis was between 3.78 and 4.93%. Cell viability assay on V79-4 Chinese hamster fibroblasts demonstrated that treatment with free CRC led to a value of 39% whereas for CRC-loaded nanofibers, the cell viability value increased to 59.66%. The results of the present study indicated that CRC-loaded electrospun nanofibers can have great potential for biomedical applications.
Szabolcs Horváth, József Gábor Kovács
Vol. 19., No.3., Pages 246-257, 2025
DOI: 10.3144/expresspolymlett.2025.19
Vol. 19., No.3., Pages 246-257, 2025
DOI: 10.3144/expresspolymlett.2025.19
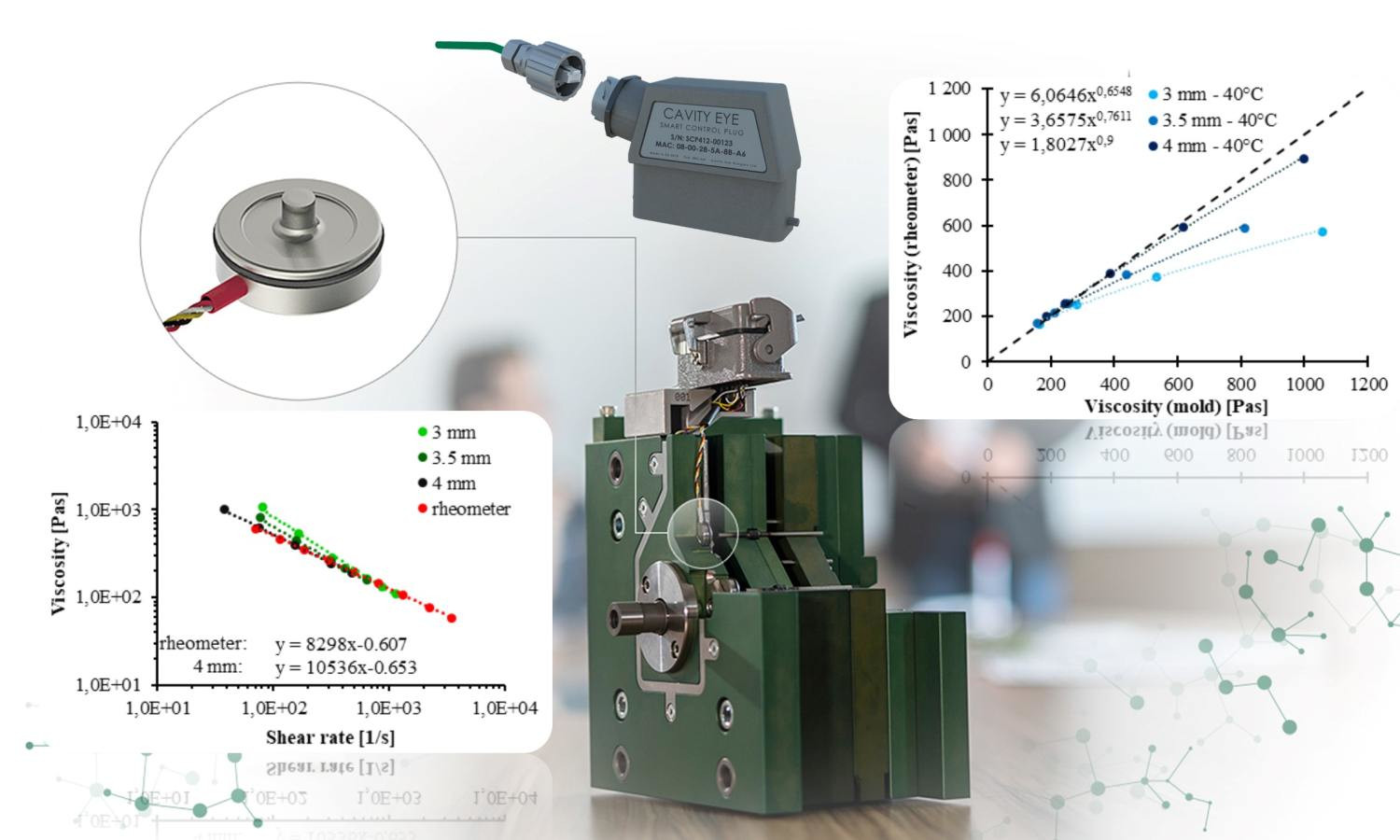
Measuring the viscosity of the melt contributes to the quality of injection molded products. Injection molding machines cannot give much feedback on the processes in the cavity, so pressure measurement inside the mold facilitates quality supervision. Our goal is to get more information about the viscosity of the material during filling in a traditional injection mold. A suitable and cost-effective method is to install cavity pressure sensors for the in-situ viscosity measurement. We prepared an experimental mold with variable wall thickness and 80×80 mm cavity dimensions. We implemented eight pressure sensors in each cavity. The wall thickness varied from 1 to 4 mm, and apparent viscosity was determined at different shear rates and mold temperatures. We measured non-isothermal and non-adiabatic flow during filling. The environment was quite different from that of standard measuring equipment. Based on the results, we effectively measured the material viscosity with a non-heated mold in the case of acrylonitrile-butadiene-styrene (ABS) and polypropylene (PP) material. The results were validated by measuring viscosity with a capillary rheometer and compared to our method using the non-heated mold, and the error was less than 10%. The results were accurate in a specific speed wall thickness range with PP and ABS.
Zaheer ul Haq, Teng Ren, Xinyan Yue, Krzysztof Formela, Denis Rodrigue, Xavier Colom Fajula, Tony McNally, Dong Dawei, Yong Zhang, Shifeng Wang
Vol. 19., No.3., Pages 258-293, 2025
DOI: 10.3144/expresspolymlett.2025.20
Vol. 19., No.3., Pages 258-293, 2025
DOI: 10.3144/expresspolymlett.2025.20
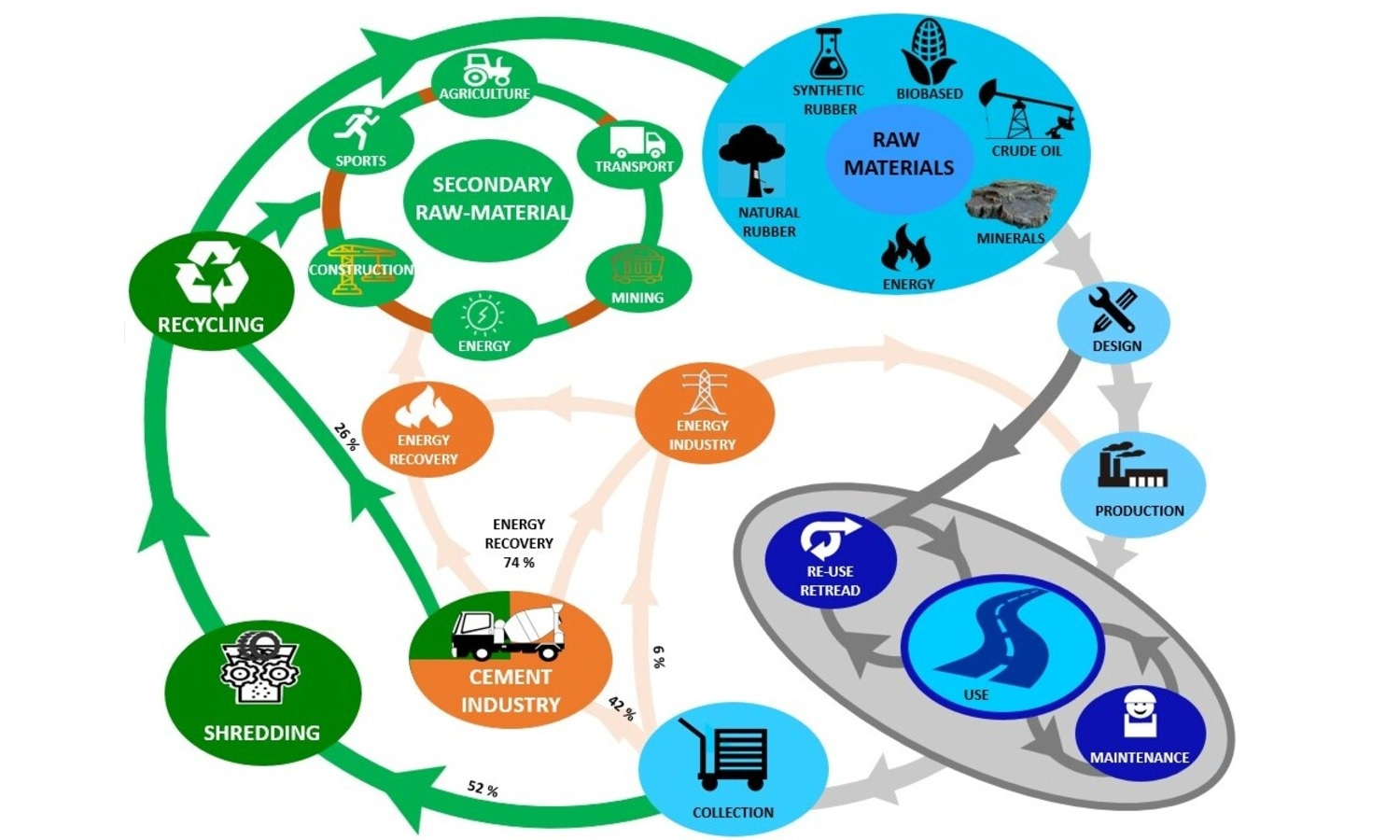
As a complex composite material, tire rubber has always presented significant environmental and waste management concerns due to its non-biodegradability and accumulation in landfills. The devulcanization of tire rubber has emerged as a historical challenge in the field of sustainable rubber engineering since Goodyear invented cross-linking in 1839. This review provides a comprehensive analysis of waste tire recycling processes, focusing on the sources, legislation, management strategies, and utilization across different regions. It explores the multifaceted challenges of devulcanizing rubber, with a specific focus on transitioning from ground tire rubber to the concept of multi-decrosslinking: sulfur bridge breakage, rubber chain depolymerization and micro-nano sized core-shell carbon black. Ideal devulcanization has restricted the release of reinforcing fillers, resulting in devulcanized rubber mainly containing dozens of micron particles, which hinder the wide usage of devulcanized rubber. This review comprehensively assesses the current state-of-the-art techniques for tire rubber devulcanization, including physical, chemical and biological methods. It explores the intricacies of ground tire rubber as a starting material, structural evolution of ground tire rubber during the devulcanization process and the associated challenges in achieving efficient devulcanization while retaining desirable mechanical properties. Furthermore, through an in-depth analysis of recent advancements, limitations and prospects, this paper offers a complete understanding of the challenges faced in tire rubber devulcanization. Considering the technical and environmental aspects of these processes, this work contributes to multi-decrosslinking, the ongoing discourse on sustainable materials development and circular economy initiatives, which pave the way for future innovations in the field of rubber recycling.
Waleed Y. Rizg, Amerh Aiad Alahmadi, Mohammed Baradwan, Rahul Dev Bairwan, Marwan M, Ahmed K. Mohamed, Sherif El Saadany, CK Abdullah, H.P.S. Abdul Khalil
Vol. 19., No.3., Pages 294-310, 2025
DOI: 10.3144/expresspolymlett.2025.21
Vol. 19., No.3., Pages 294-310, 2025
DOI: 10.3144/expresspolymlett.2025.21

This study investigated the development of thermoplastic composites by incorporating crude lignin extracted from coir fiber waste, into poly(3-hydroxybutyrate-co-3-hydroxyvalerate) (PHBV), a biodegradable polymer. The extracted crude lignin was blended with PHBV as a matrix, and spent coffee grounds (SCG) were used as biofillers. SCG were chemically modified through sodium hydroxide (NaOH) treatment and maleic anhydride (MA) grafting to enhance their compatibility with the PHBV/lignin blend. Raw and modified SCG were characterized for their functional, morphological, and thermal properties before being incorporated. Thermoplastic biocomposites were prepared via melt compounding and compression molding and evaluated for water barrier, morphological, mechanical, and thermal properties. Results showed that MA-grafted SCG significantly enhanced PHBV-lignin properties, increasing tensile strength by 23.7% and thermal stability by 11.9% compared to the control matrix. Optimal performance was observed at 5% MA-grafted SCG filler loading. However, higher SCG concentrations (7%) led to filler agglomeration, negatively affecting the material properties. This research demonstrated the potential of utilizing agricultural and food waste to create high-performance thermoplastic composites for future applications in biodegradable packaging, contributing to the advancement of a circular economy and environmental sustainability.
Wenxin Gan, Hanyu Xue, Hongyi Lin, Renjin Gao, Yuchi Zhang, Liwei Wang, Jiuping Rao
Vol. 19., No.3., Pages 311-325, 2025
DOI: 10.3144/expresspolymlett.2025.22
Vol. 19., No.3., Pages 311-325, 2025
DOI: 10.3144/expresspolymlett.2025.22
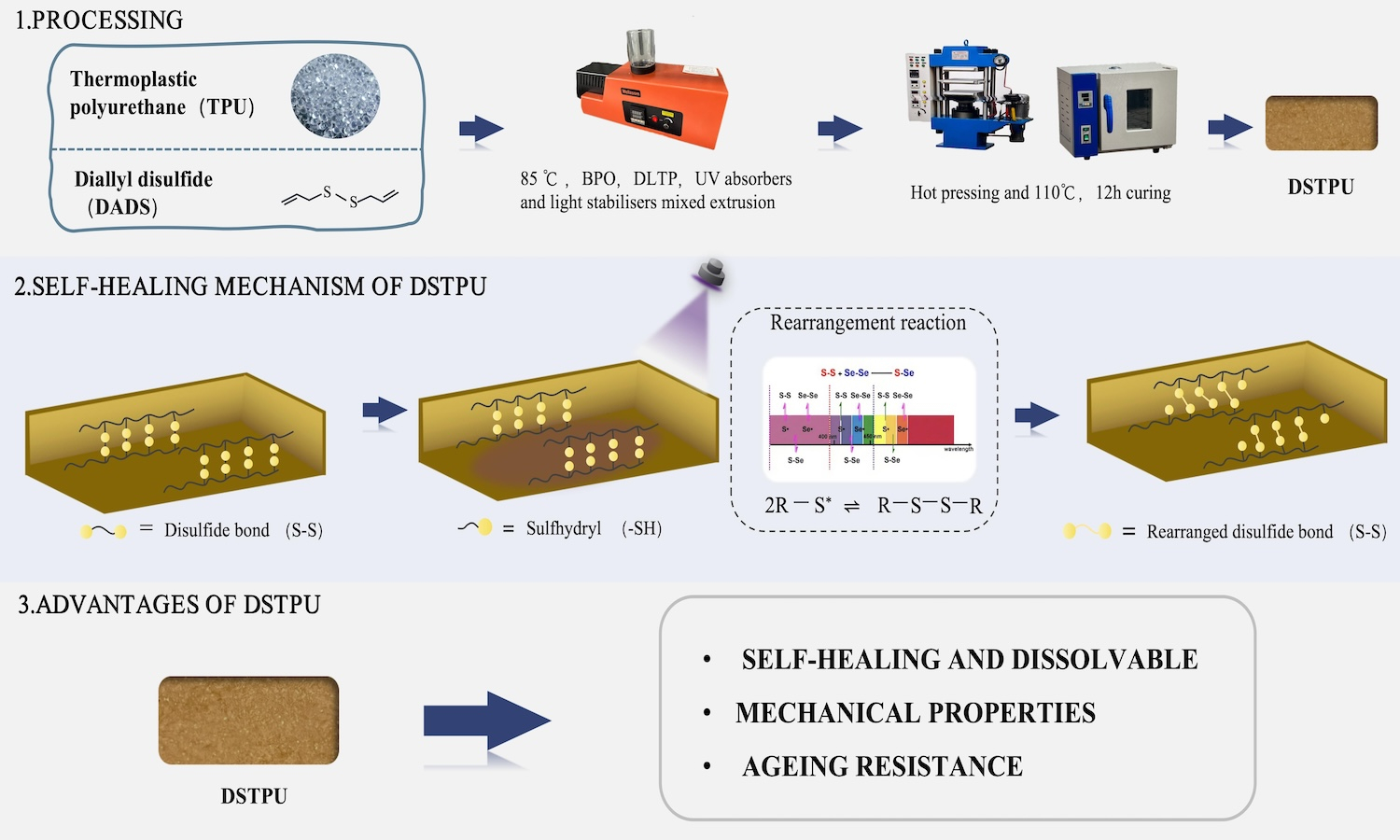
Cross-linking frequently enhanced the mechanical properties of linear polymeric materials; however, it also resulted in the transition from thermoplastic to thermosetting materials, which posed issues from an environmental perspective. Thermoplastic polyurethane (TPU) elastomers were extensively applied across various industries. To improve the mechanical properties of TPU while preserving its environmental benefits, this study integrated radical copolymerization technology to develop a reversible crosslinked TPU. Specifically, the linear polyurethane molecular chains were crosslinked using diallyl disulfide (DADS) as a functional cross-linking monomer. Through radical copolymerization reactions, reversible crosslinks formed from disulfide bonds were created between the linear polyurethane molecular chains, yielding a self-healing reversible crosslinked thermoplastic polyurethane (DSTPU). The study showed that DSTPU could self-heal and dissolve under UV light and alkaline N,N-dimethylformamide (DMF) conditions, achieving 82.2% self-healing efficiency at 3 phr DADS. It dissolved into fine particles in alkaline DMF. Disulfide bonds in DSTPU enhanced cross-linking, boosting 19% oxygen permeability, thermal conductivity (0.218 W/(m·K)), and mechanical properties like tensile stress (11.18 MPa), force (134.13 N), and elongation (548%). These bonds also enhanced aging resistance, cutting ΔYI to 6.0%.
Sarahí Bautista Reberte, Esmeralda Zuñiga Aguilar, Solange Ivette Rivera Manrique, Carlos Alberto Martínez-Pérez
Vol. 19., No.3., Pages 326-338, 2025
DOI: 10.3144/expresspolymlett.2025.23
Vol. 19., No.3., Pages 326-338, 2025
DOI: 10.3144/expresspolymlett.2025.23
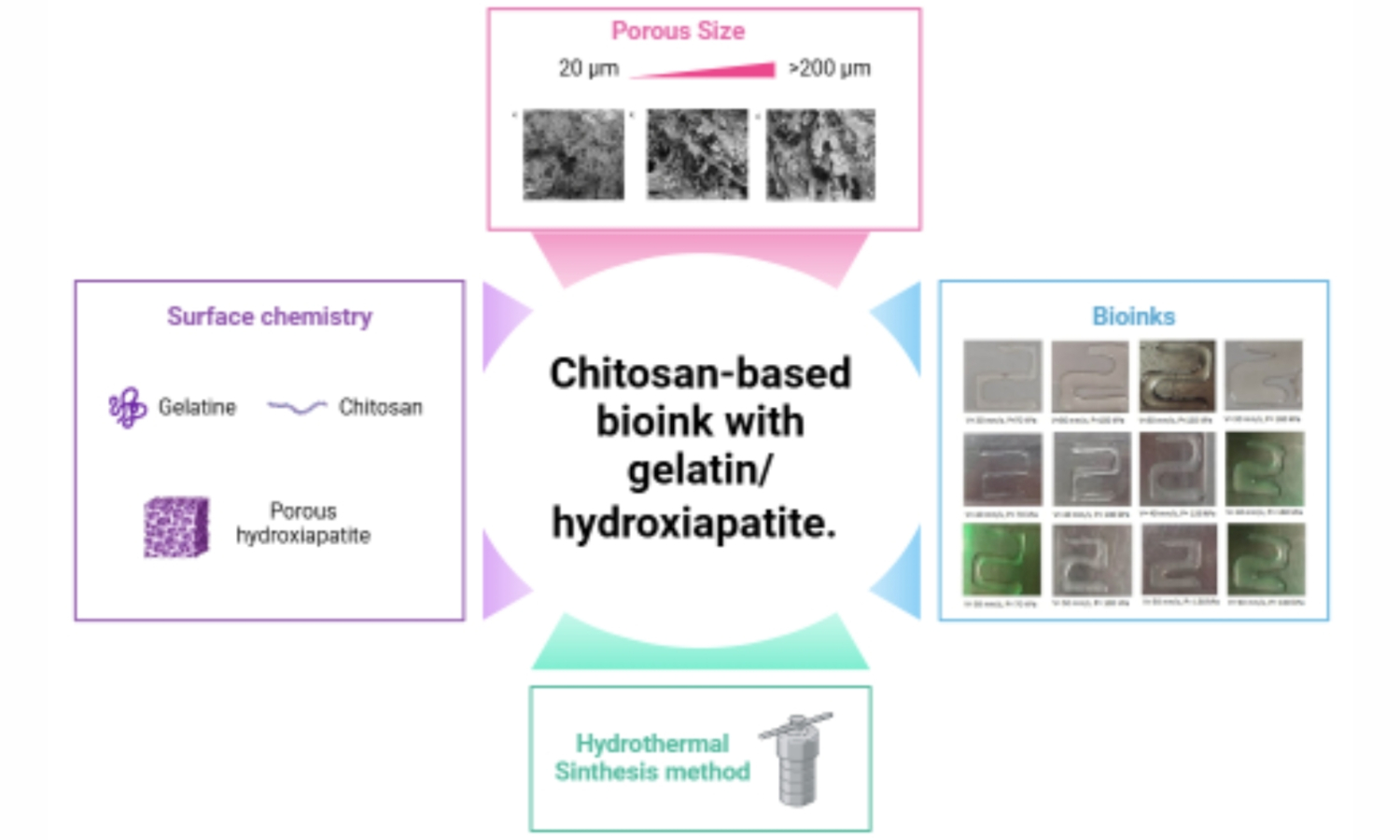
Three-dimensional (3D) bioprinting is a technique currently used for creating tissue engineering scaffolds, using bioinks as the building blocks. These bioinks are composed of biomaterials that provide structural integrity and are synthesized from organic polymers to enhance biocompatibility with the printed constructs. In this study, a series of eleven chitosan-based bioinks were synthesized using the sol-gel technique, employing chitosan of low and medium molecular weight. Three bioink formulations were selected based on their viscosity characteristics and further enriched with gelatin and hydroxyapatite (HA) to enhance their mechanical properties. Characterization tests included Fourier-transform infrared spectroscopy (FTIR), thermogravimetric analysis (TGA), scanning electron microscopy (SEM), and rheological assessments. Viscoelastic materials were obtained, and an experimental model was developed to optimize printing parameters, focusing on pressure and printing speed. Our findings indicate that a bioink formulation comprising a blend of medium and high molecular weight chitosan, supplemented with gelatin and hydroxyapatite, was found to be a promising approach for fabricating scaffolds for bone tissue repair.
Nabil Hayeemasae, Sitisaiyidah Saiwari, Siriwat Soontaranon, Mohamad Irfan Fathurrohman, Abdulhakim Masa
Vol. 19., No.3., Pages 339-349, 2025
DOI: 10.3144/expresspolymlett.2025.24
Vol. 19., No.3., Pages 339-349, 2025
DOI: 10.3144/expresspolymlett.2025.24
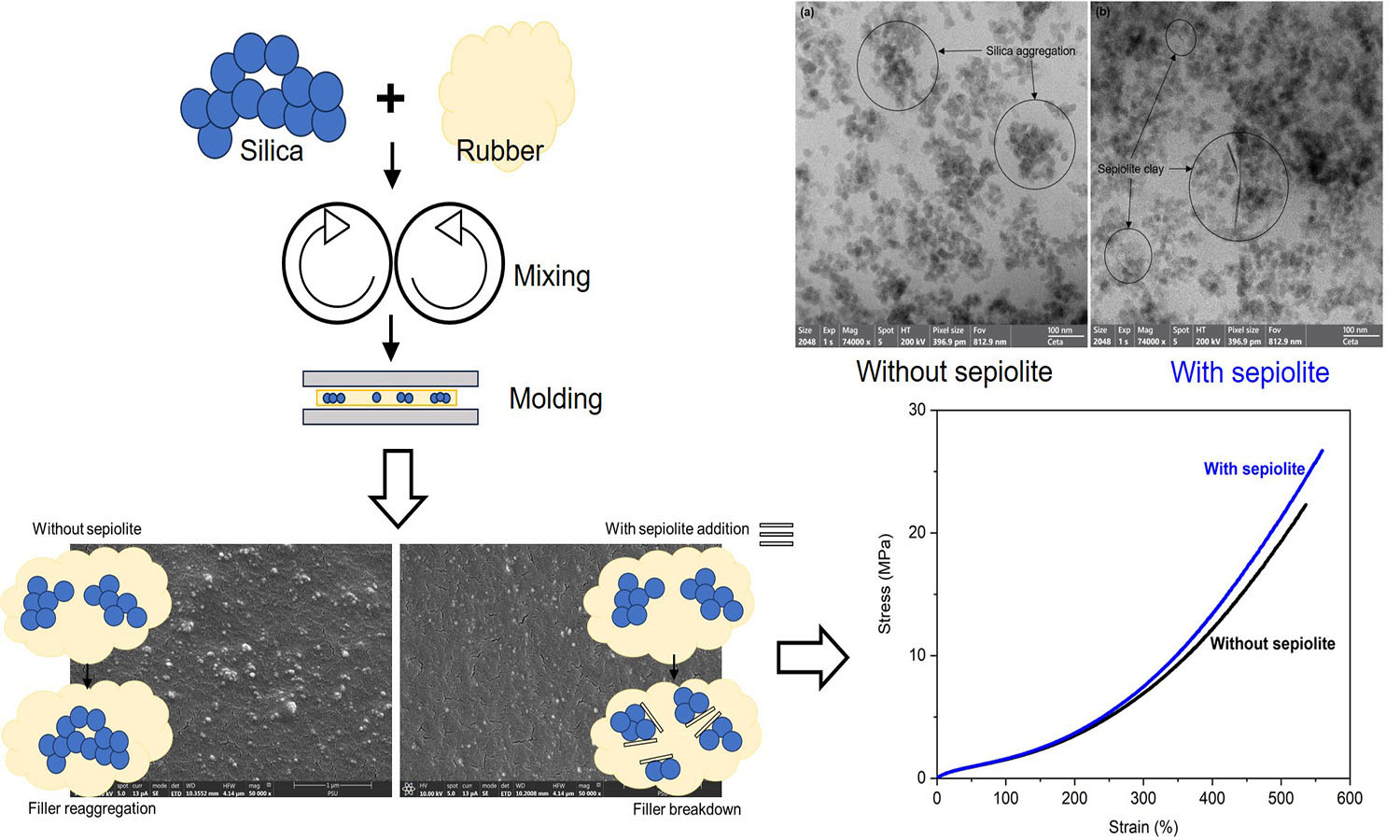
Natural rubber (NR) composites filled with silica and crosslinked with phenolic resin were prepared in this study. The influence of a small sepiolite addition (1–5 part(s) per hundred parts of rubber, phr) on the properties of NR composites was studied. It was found that sepiolite reduced silica aggregate size, allowing improved dispersion in the NR matrix. Sepiolite facilitates silica dispersion by locating at the silica surfaces and acting as a barrier that prevents agglomeration of silica filler. The swelling resistance, crosslink density, tensile strength, and strain-induced crystallization were all strengthened by incorporating sepiolite because of the improved silica dispersion. The greatest tensile strength was achieved at a 2 phr sepiolite addition level. The improvement was about 18% over the reference composite due to the greatest filler-rubber interactions and the finest filler dispersion. The results clearly indicate that sepiolite clay can be applied as a dispersing agent in silica-containing rubber composites.